3D printing for seals
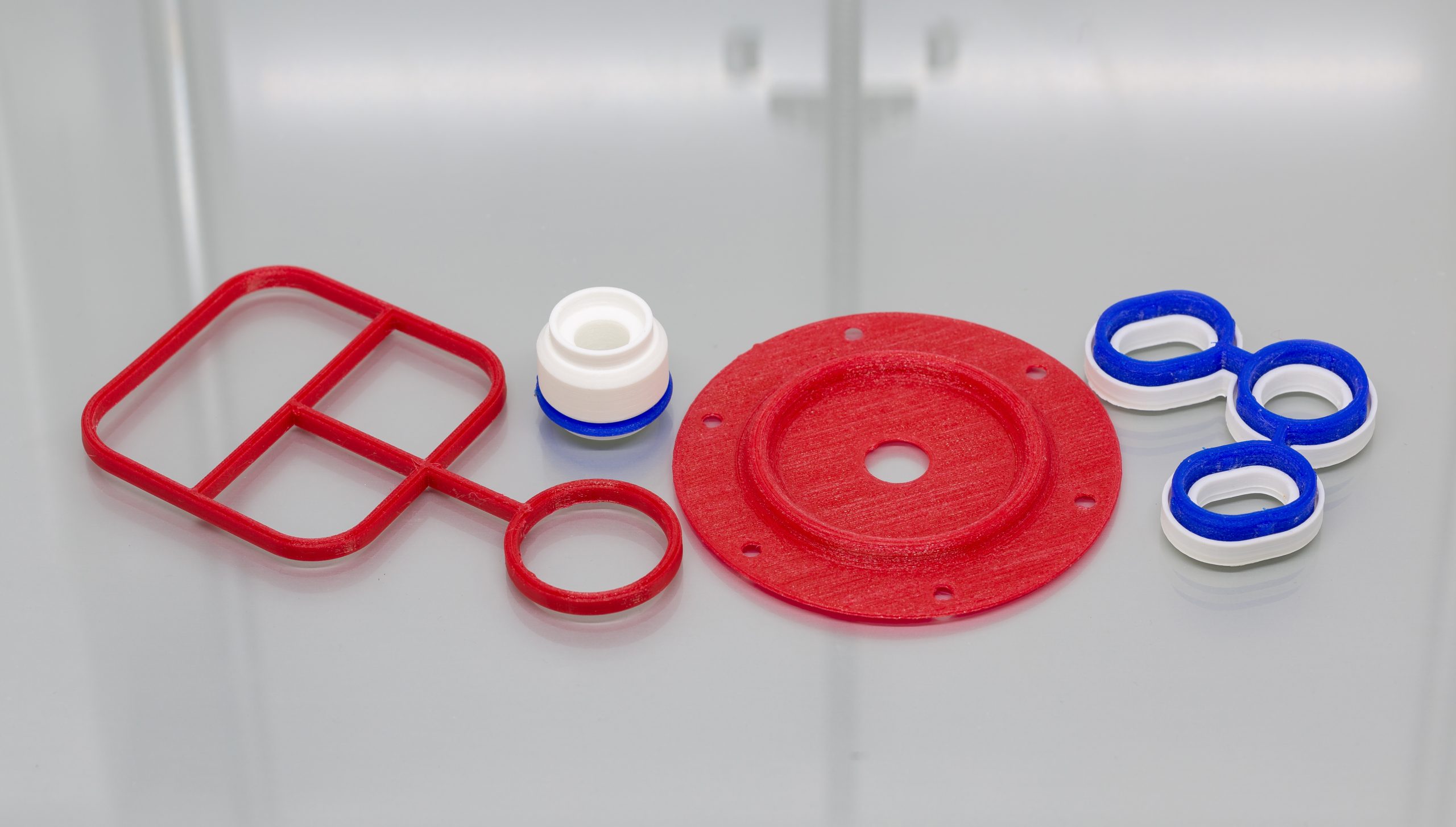
What is 3D printing?
3D printing is typically the more common name used for additive manufacturing. This process involves the construction of a three dimensional shape that is designed and generated from a computer aided design program (or CAD). The most typical process used for 3D printing is FFF (Fused Filament Fabrication) or FDM (Fused Deposition Modelling).
The FDM process uses a continuous filament of a thermoplastic material that is then deposited onto the 3D print bed, creating layer by layer and gradually building up the structure of the 3D model.
This is the process we commonly use to create our design and development range of 3D printed models and seal prototypes.
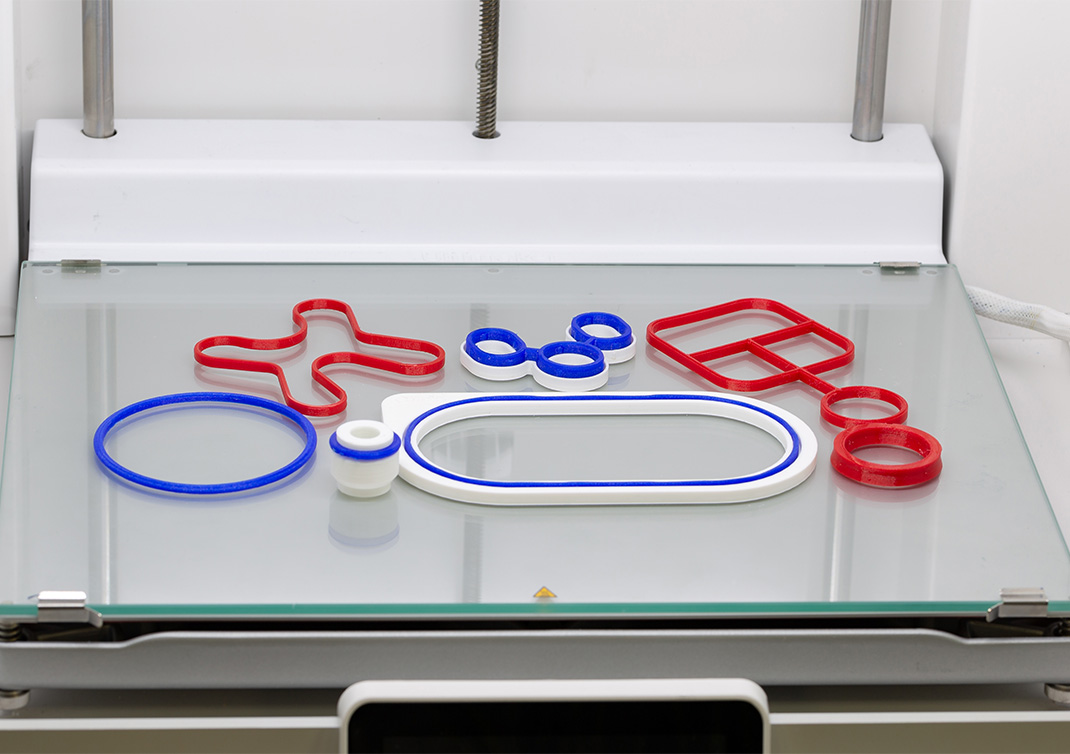
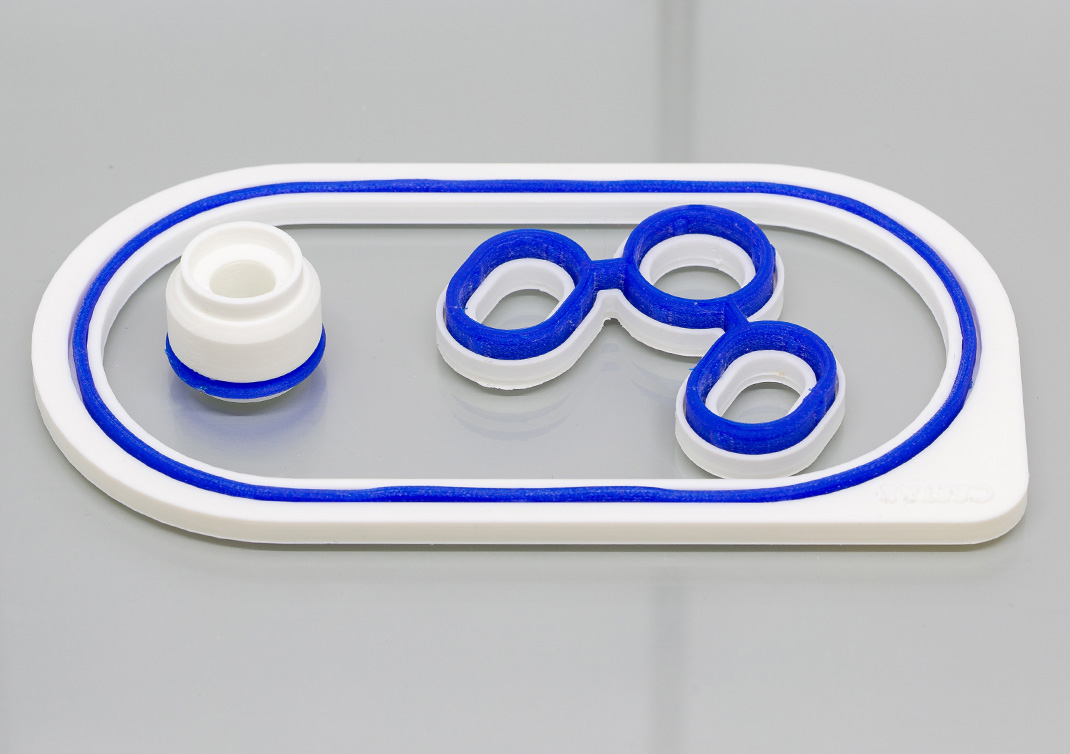
What material is suitable for 3D printing?
The materials used for 3D printing must of course be compatible with the process – these include a range of thermoplastic grades. Typical suitable material grades include; Polylactic acid (PLA), Acrylonitrile Butadiene Styrene (ABS), Thermoplastic Polyurethane (TPU), Nylon and Polypropylene (PP).
The most common grade we use for 3D printing is PLA – for its great strength and stability. We’ve also adapted our design process to use more TPU based material grades, as it loosely demonstrates the same properties as elastomer grades and is better for using in prototype programmes where mechanical fit in groove is tested.
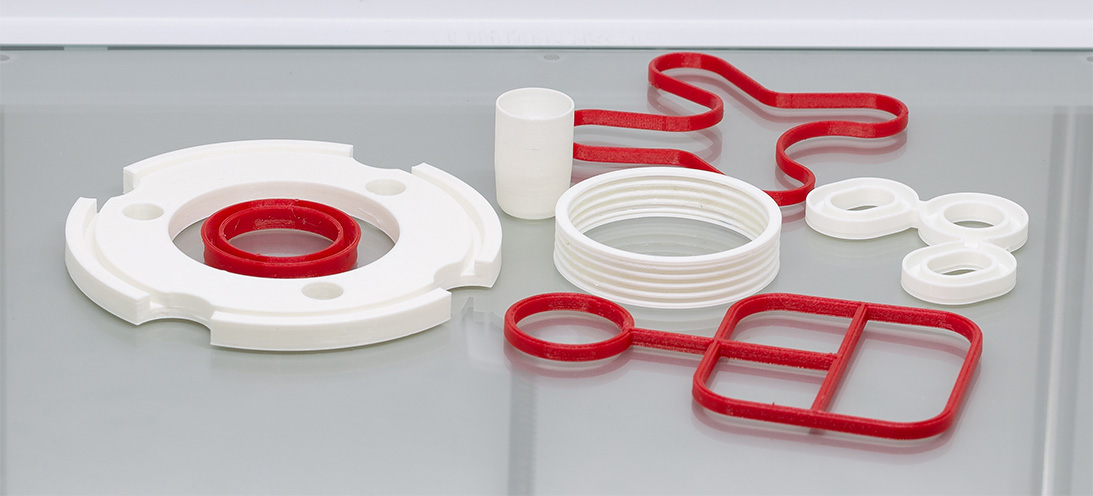
Why use 3D printing for seals?
3D printing can be used for a variety of designs and seal types; from O-rings, gaskets and lip seals – to grommets, multi shot mouldings and large seal assemblies.
There are many benefits of using 3D printing during the initial design stages of a project. The rapid turnaround means that a simple seal design can be produced in around 15 minutes, and even more complicated parts can be manufactured in the same day. We can even print the application housings and it’s the perfect way to demonstrate to an engineer what they can expect from a seal part in terms of shape and fit for hardware without the lead time and cost of cutting a prototype tool for moulded parts.
One example of this is by quick turnaround of gasket designs typically to suit automotive applications or similar critical markets. Our engineers can design the concept and then 3D print a rapid prototype of a gasket to suit a 3D printed gauge groove.
This further demonstrates to the customer that the seal has been fit checked for installation and builds further confidence in the design recommendation. Our engineers combine the 3D print with FEA simulation reports to offer a fully engineered sealing solution.