Seals for electric vehicles
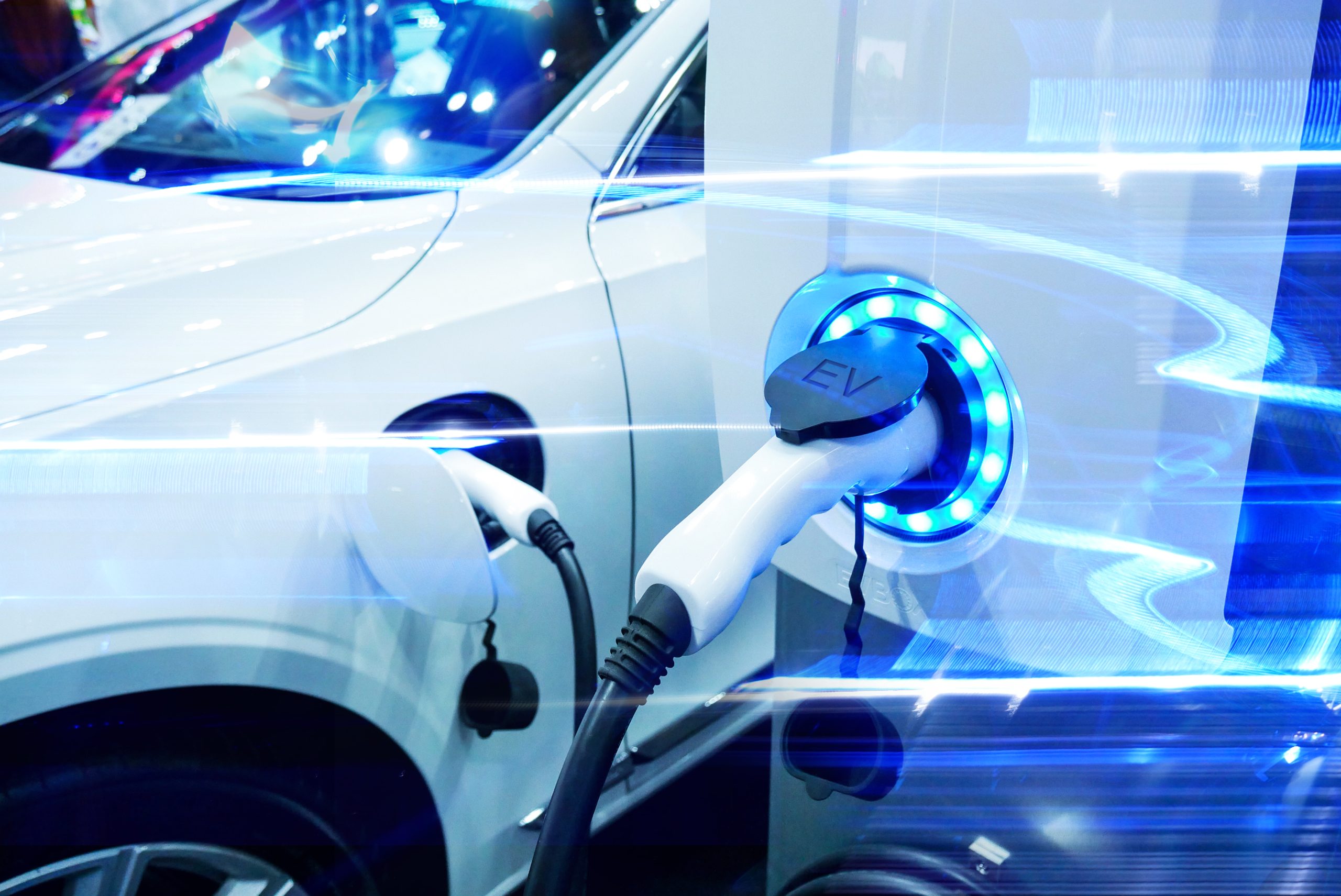
Hybrid and hydrogen vehicles
Hybrid vehicles have a petrol (or diesel) engine combined with an electric motor and relatively small battery and feature all the traditional areas of automotive applications that require seals including oil, steering, suspension and braking systems.
They also require seals for environmental and RFI/EMI (Radio Frequency Interference /Electro Magnetic Interference) applications. These are normally gaskets required for a number of electronic control, junction and connection boxes (for power invertors, charging electronics, motor and battery enclosures). These are generally placed around the vehicle, but batteries tend to be under or behind the back seat and sometimes the fuel tank is smaller and the battery sits in a similar place.
Application characteristics also include high speed rotary sealing requirements around the output shaft of the motor and potentially in the gearbox that links in with the combustion engine drivetrain.
Plug-in hybrid vehicles have gaskets or seals (environmental and/or shielded) associated with the cable charging connection.
Hydrogen Fuel Cell
These vehicles have no combustion engine, and the fuel cell is often located where the petrol engine would be. Electrical power is produced by passing hydrogen and oxygen gasses through a “battery” (the cell) with anodes and cathodes which produces electricity that drives the motors and is also stored in more conventional hybrid style.
Waste product is water and warm air; this is very environmentally friendly (more so than pure battery power which uses electricity often generated in a “non-green” way and which also consumes rare earth minerals such as lithium).
There are traditional automotive seals in areas of applications such as steering, cooling, suspension, and braking systems, as well as environmental and RFI/EMI shielding gaskets and high speed rotary seals requirements.
Hydrogen gas is normally stored in a tank at up to 700 bar pressure and again is usually situated just behind, or under the back seat, and requires sensors, valves and pressure regulators to operate. There are seals and gaskets required within the fuel cell itself, these require H2 resistance. Some fuel cells have small compressors which force the gasses through the fuel cell at higher pressure for improved efficiency, and then expanders which recover energy from this gas flow at the exhaust of the fuel cell. These often require high speed rotary seals (generally PTFE materials) and they run unlubricated.
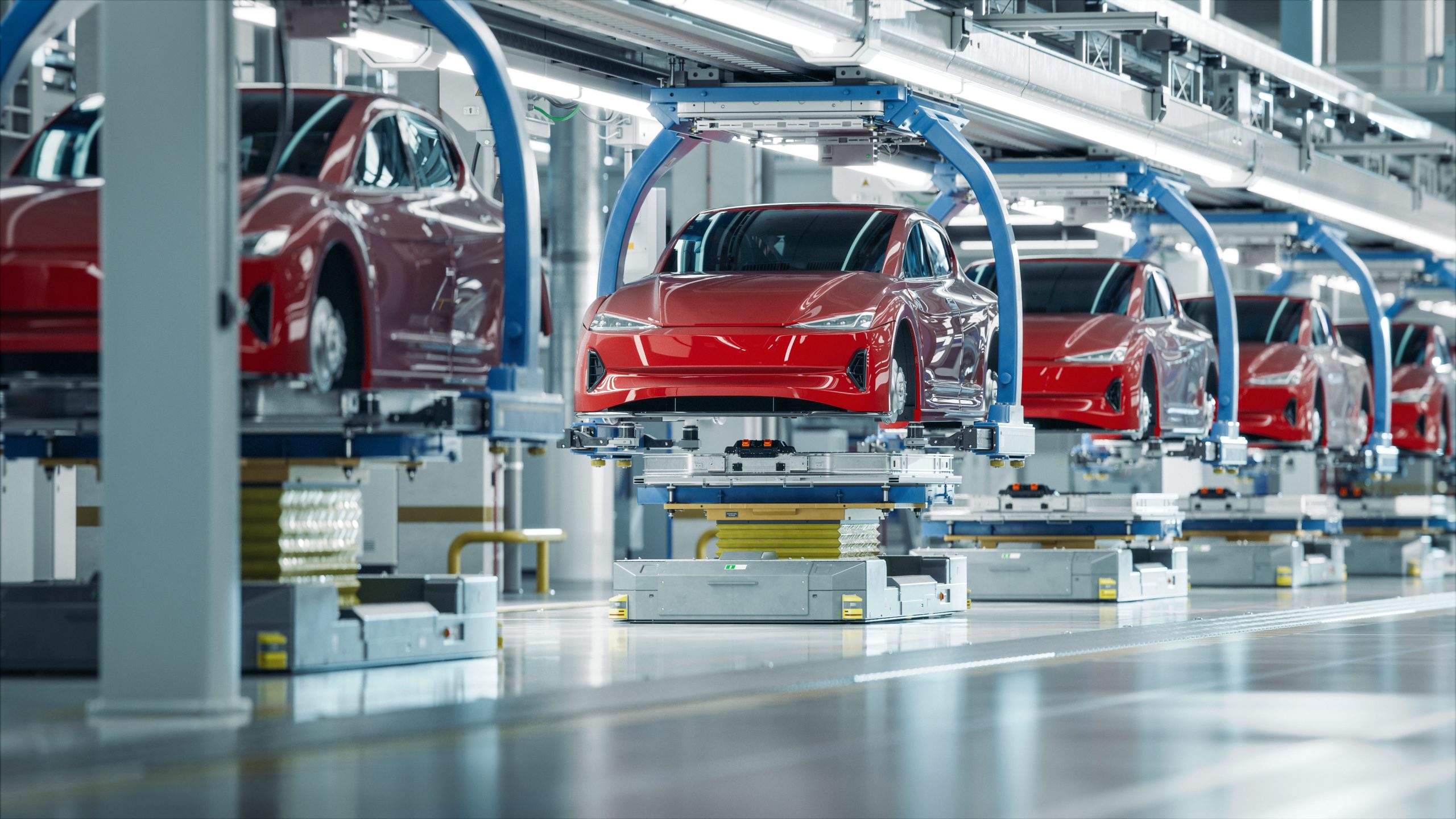
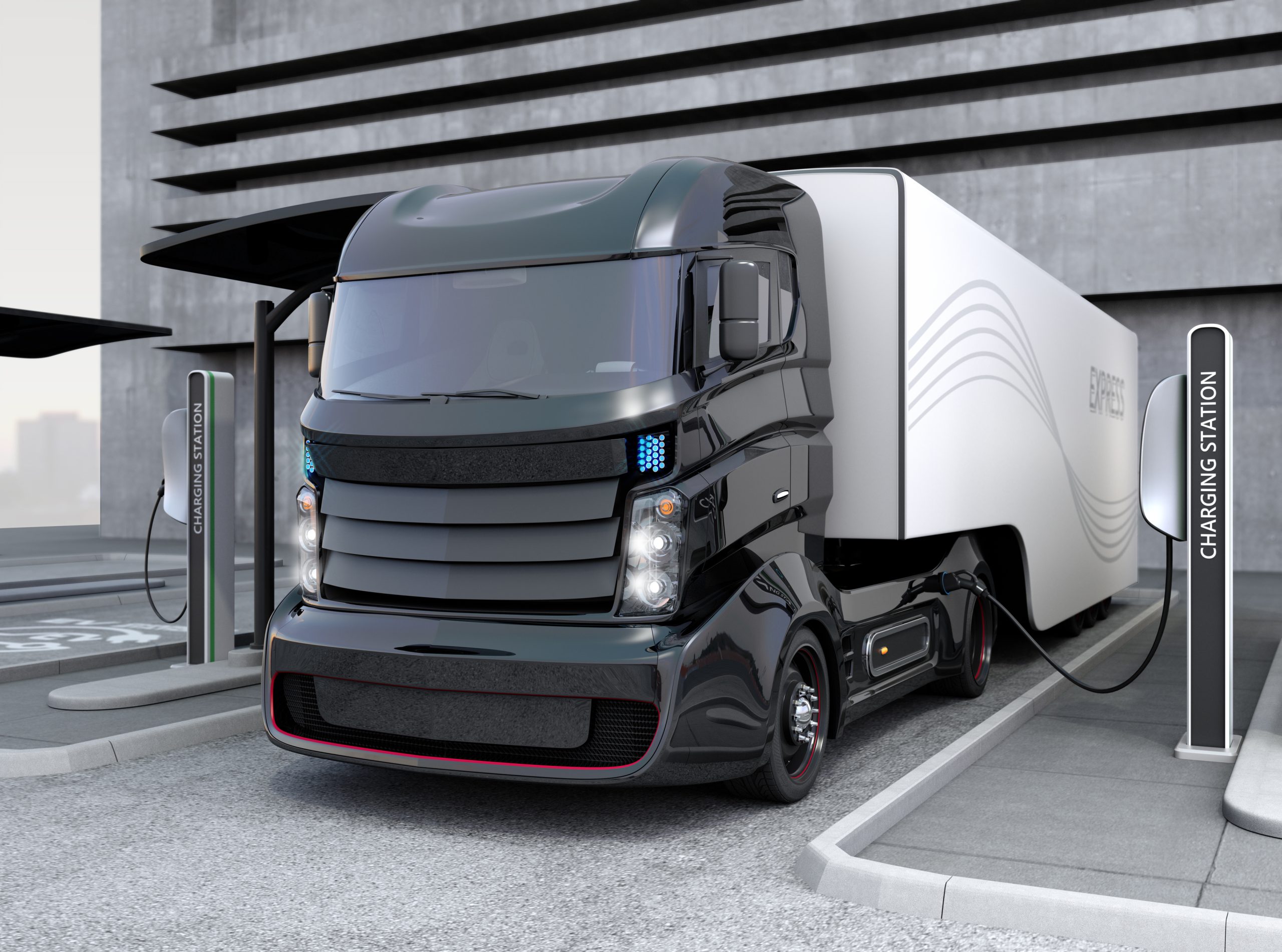
Battery applications
Full battery electric
These vehicles have large batteries that typically take up the entire floor area underneath all of the seating compartment of a car. As with other EV’s there are the traditional seals in automotive areas; no oil system, but the steering and cooling systems, for the battery itself and the suspension and brakes. There are also environmental and EMI/RFI shielding gaskets and high speed rotary sealing requirements. The plug in charging ports also present a sealing application.
Filling and charging
There are many different applications for filling and charging. Home charging points are normally smaller and wall mounted for domestic use, while commercial and forecourt charging will encompass hydrogen filing. There are all similar application types as already mentioned including shielded and environmental gaskets for the electric applications and hydrogen sealing for the H2 filling applications.
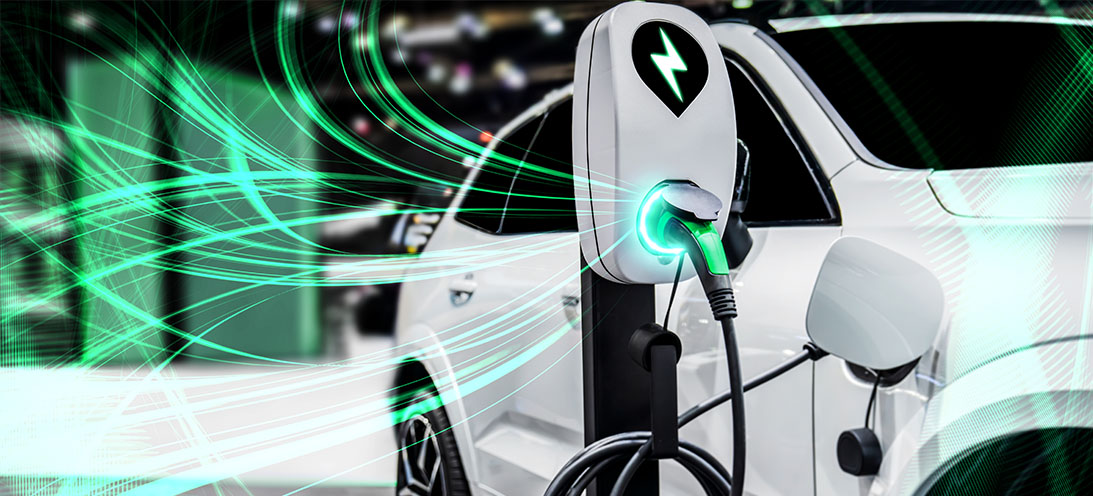
Design & Development for Electric Vehicle applications
Our engineering team understand the demands associated with automotive applications, and we support vehicle manufacturers by designing innovative sealing solutions for electric vehicle applications.
We use the latest in 2D/3D CAD and FEA simulation software to design and replicate automotive seal performance before finalising each individual seal design, incorporating significant feature and critical function elements for integration with customer mating parts. We offer material development and testing, and a component endurance testing service.