Why use metal seals?
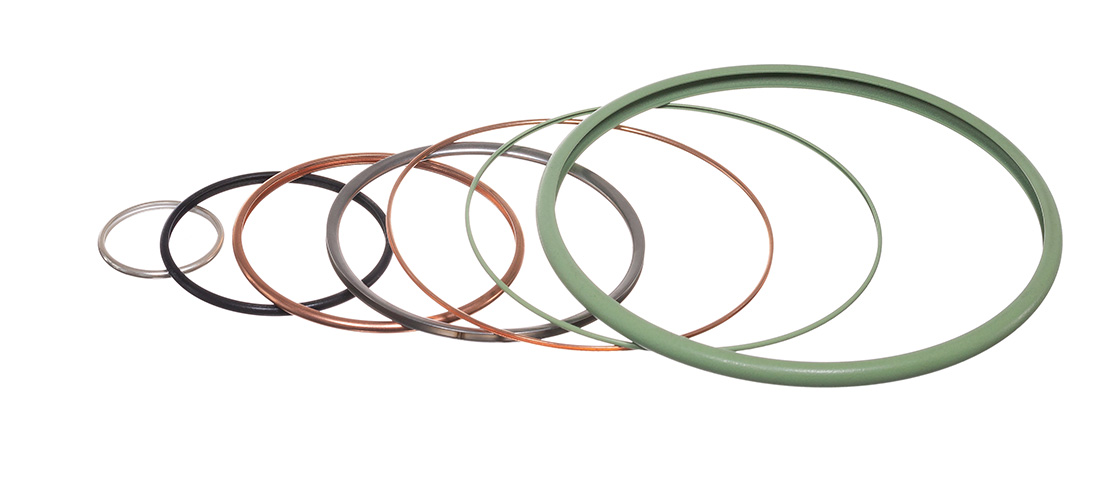
How do metal seals work?
The metal seal concept is based on plastic and elastic deformation of the seal during compression which creates a sealing interface. The metal seal is compressed in the cavity on average about 20% of its original free height and the force generated through compression of the ring produces a high contact stress at the seal/cavity interface. This force is then supplemented by the pressure-energisation force which rises in proportion to the increase in differential pressure inside the seal cavity.
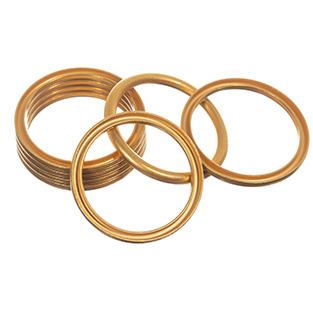
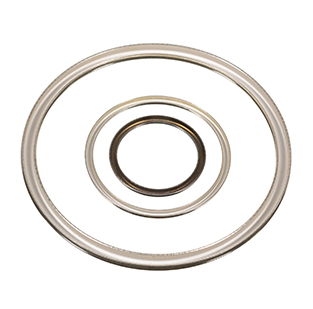
What types of metal seal are there?
There are three types of seal energisation; self, spring and pressure energisation. By design metal C-rings are self-energising due to the good spring back characteristic of the C-shaped profile, and they can be used in internal, external and axial pressure conditions. The different base material characteristics and heat treatments, along with material thickness and cross section of the seal also determine the compressive load and this is directly related to the sealing level achieved and is known as “self-energisation”. Spring energised seals have excellent spring back properties and are typically used to improve leakage rates by increasing the load on the sealing interface.
All metal seals can use system pressure to generate a hydrostatic load to obtain the highest level of sealing possible; this is known as pressure energisation. At high pressures this becomes an advantage and allows the design of metal seals for applications of 25,000 PSI and above.
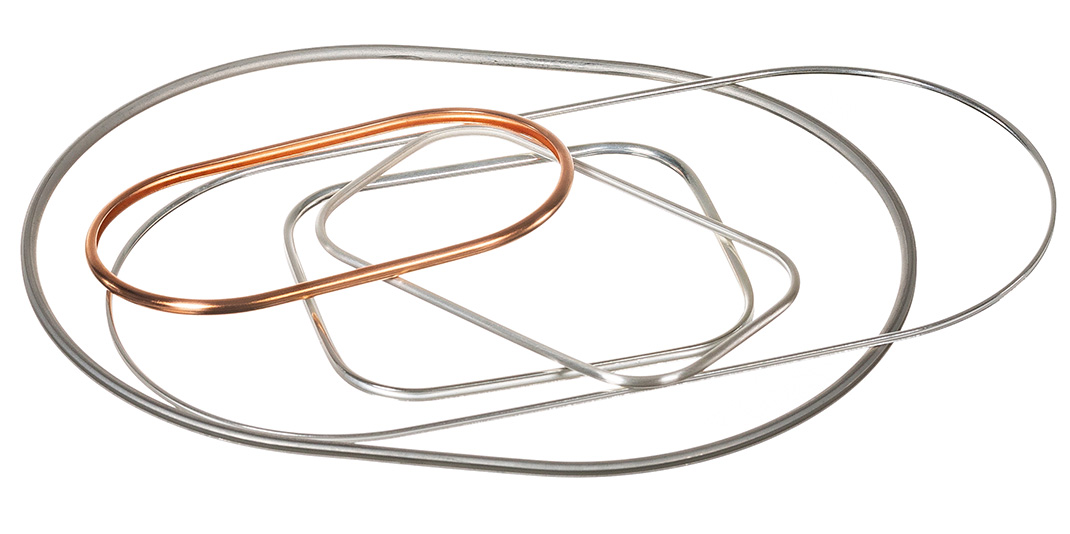
Ultimate seal performance
Once the metal seal profile and material has been selected depending on the application, there are a variety of platings and coatings available to modify the surface properties of the seal to create a malleable outer surface layer. Typically precious metals such as gold and silver are used for plating, but many other options are available with two common ones also being Tin or PTFE. This layer ensures optimum sealing despite any mating surface imperfections. The plated or coated layer also reduces coefficient of friction so the seal can slide and bed down during initial compression, therefore preventing galling. As well as providing better physical properties to the seal, coatings and platings are chosen to withstand high temperatures and aggressive (often corrosive or oxidizing) environments.
With ever changing industry demands and fast paced technology developments – particularly from our customers in the Oil & Gas, Aerospace & Defence and Automotive markets – we are challenged daily with applications where the boundaries are being pushed to the absolute limit. We have designed metal seals into F1 car exhaust systems, subsea repeaters, oil and gas production valves as a few examples; the capabilities of high performance metal seals is endless. Working with the latest developments in materials, platings and manufacturing technology; our engineering team design the sealing solutions to meet the complex specifications these types of application demand.