Why use PTFE seals?
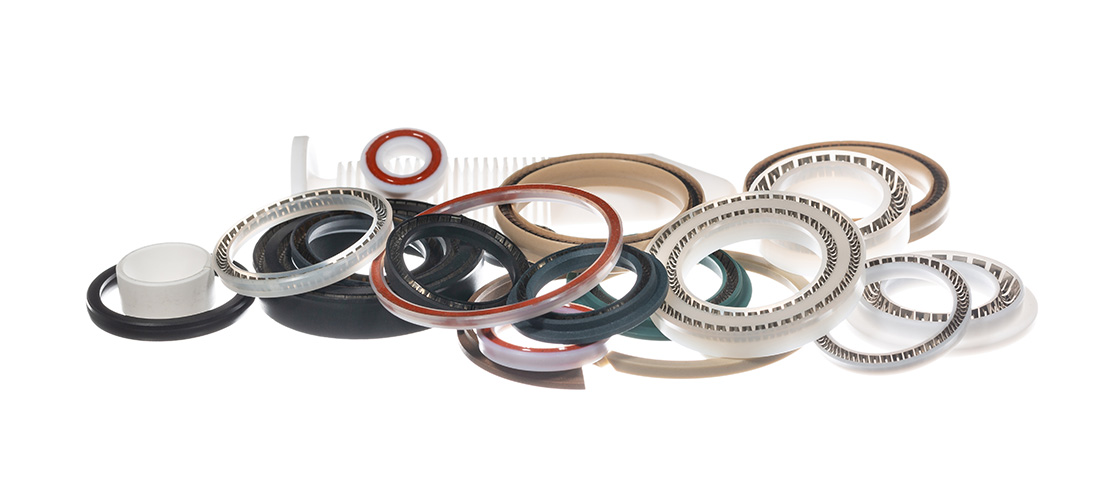
What is PTFE?
Discovered accidentally in 1938 in the DuPont™ laboratory in Jackson, New Jersey, USA, the molecular structure of PTFE is based on a linear chain of carbon atoms which are completely surrounded by fluorine atoms. The carbon-fluorine bonds are among the strongest occurring in organic compounds and as a result PTFE has thermal stability across a wide temperature range.
It’s high melting point (342 °C) and morphological characteristics allow seal components made from virgin PTFE to be used continuously at service temperatures of up to 260 °C, and with the addition of fillers – up to 300°C. It has the unique ability to resist material degradation, heat-aging and alteration in its physical properties during temperature cycling. Alongside this rare combination of material characteristics PTFE also has unlimited shelf life.
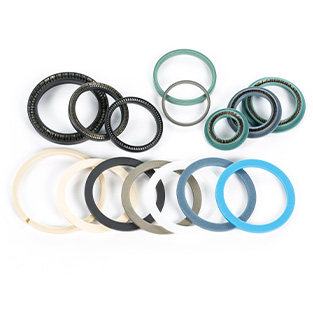
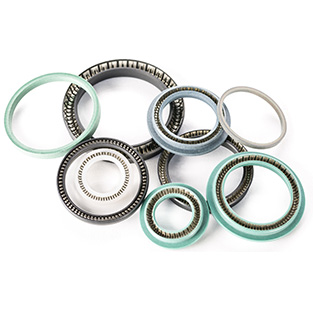
Why use PTFE seals?
Notably PTFE demonstrates extraordinary chemical resistance: the intrapolymer chain bond strengths preclude reactions with most chemicals, thereby making it chemically inert at elevated temperatures and pressures with virtually all industrial chemicals and solvents. Only a few media (some molten alkalis) are known to react with PTFE seals making them the perfect sealing solution for highly aggressive chemical applications.
PTFE also has the lowest friction coefficient of any known solid; it has self-lubricating capabilities which offers continuous dry running ability in dynamic sealing applications and has superb stick/slip capabilities.
Focus on dry coatings
The advantages of using PTFE in sealing applications are; functionality at high and low temperatures, dynamic sealing with high wear capabilities, high pressure sealing (using combinations of PEEK back-up rings) and compatibility with highly aggressive chemical combinations.
Our range of PTFE seal products include back-up rings, rod and piston seals, slipper seals and spring energised seals in a wide variety of sizes. Materials depend on application requirements but we offer a wide range from Virgin PTFE or including filler combinations of MoS2, glass, carbon, carbon fibre, graphite, and bronze.
These characteristics make PTFE seals perfect for the demanding applications involved in Oil & Gas, Aerospace, Automotive and Chemical Process markets (to name but a few) and Ceetak’s engineering team are experienced in the design of PTFE sealing solutions to meet the complex specifications these types of application demand.