Moulded gaskets for an automotive application
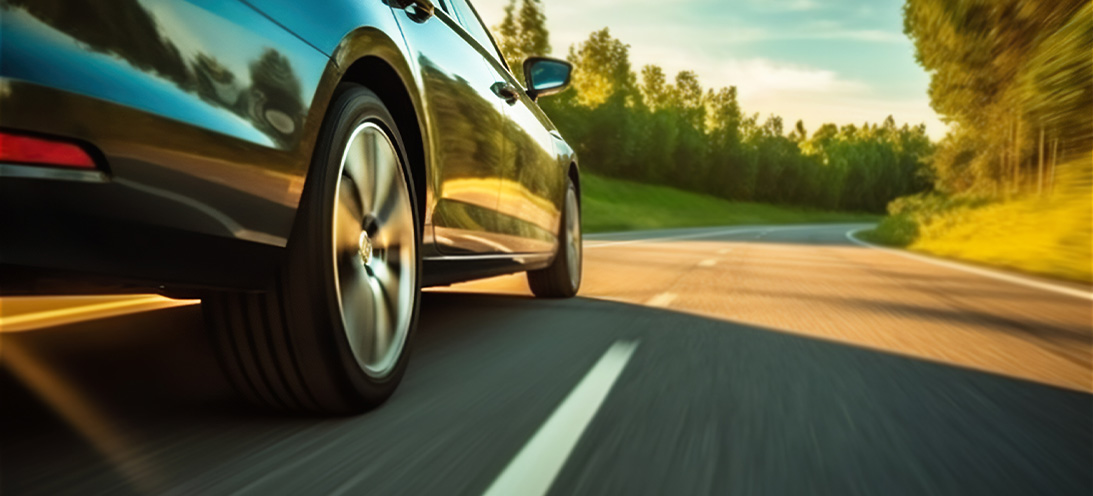
The application
This gasket is used within a valve housing in an automotive application. The original competitor gasket was experiencing failure at the “T-junction” areas of the seal; our customer had experienced chronic failures of their existing design at high temperatures and high pressures.
The seal was required to perform under pulsating pressure of up to 50 Bar and temperatures of up to 150°C. Our engineers reviewed the existing gasket design and application conditions and recommended an increase in height of 0.40 mm.
This was to increase the compression and improve the sealing function. Additional beads were also added to further stabilise the gasket in the groove.
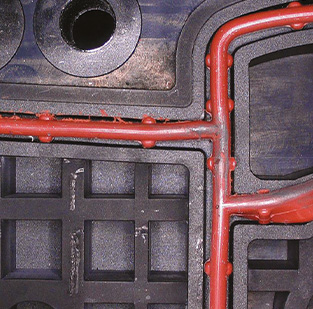
The challenges
Prototype parts were manufactured from a single cavity soft tool and sent to the customer for in-house testing and validation. The prototype gaskets very nearly passed testing but did not quite reach the 50 Bar pressure requirement at 150° C (42 Bar reached). This was still a great improvement on the performance of the customer’s original gasket.
We analysed the customers test data and reviewed images of the tested parts, and determined that there were areas where the gasket was sliding in the groove and then shearing as the pressure pulsed. To resolve this issue, our engineers added beads to the rear of the T-intersections of the gasket. This provided additional support and further stabilised the gasket at the high-pressure stress points in the groove, thus reducing the amount of movement within the housing.
The number of additional beads added needed to be balanced carefully with calculations on groove fill. Further development captured the cleanliness requirements and altered radii on the beads.
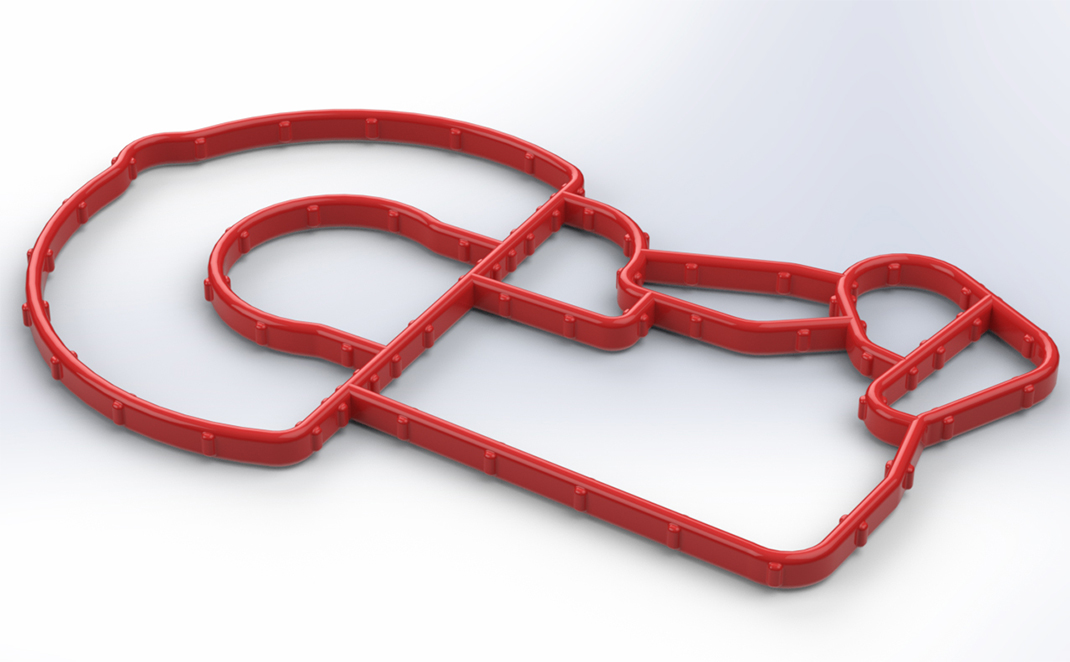
Customer satisfaction
The new design was approved, and the customer moved to production tooling stage and sample parts were produced to PPAP Level 3. These parts have since been approved and full production quantities have been ordered manufacturing builds in 2022.