Are all elastomers the same?
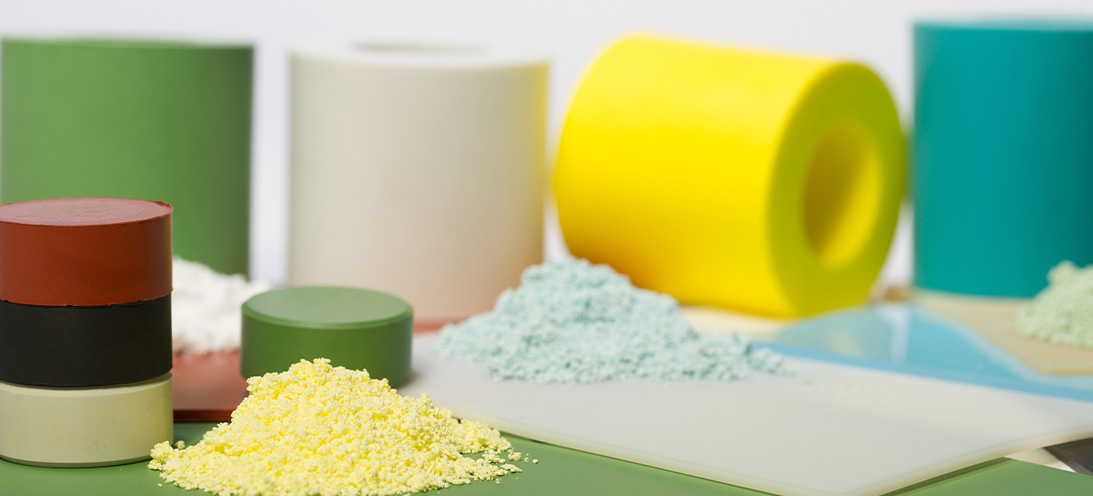
Material hardness
This is often the least considered property when selecting a material, but in sealing applications elastomer material hardness can impact assembly loads, seal friction and extrusion resistance. Softer seal compounds can be used effectively against rough hardware surface finishes, as the softer rubber can better accommodate surface imperfections (especially when sealing low pressure gas). Harder compounds will have greater wear resistance in dynamic applications.
Most of the common base elastomers are produced in 60 to 80 Shore hardness range, and tend to be produced in increments of 5 hardness points. It’s important to remember that the hardness tolerance of a material is typically +/-5 points, so both 70 and 80 hard nominal materials could both legitimately have a hardness of 75 Shore A.
With possible hardness down to 30 Shore A (or even lower), silicone rubber lends itself to applications requiring very soft seals. An example of which is where seal compression forces need to be low to enable easy manual assembly of components. NBR, HNBR and FKM materials can be formulated up to 95 Shore A hardness for highly demanding high pressure and temperature applications; for example applications found in the Oil & Gas industry.
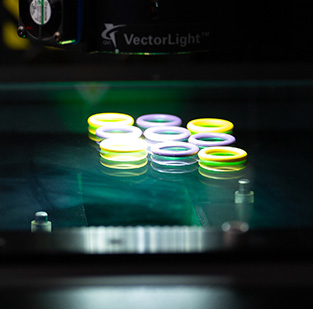
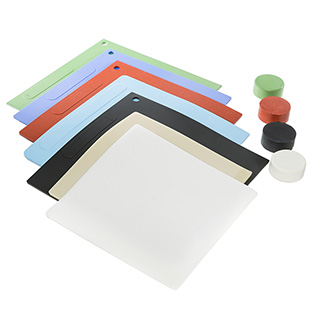
Chemical compatibility
Unlike PTFE seals (where there are very few chemicals that will attack and breakdown the material) elastomer seal materials have to be carefully selected so that the properties are not affected by any fluids or gasses that the seals come into contact with. This includes not only the main media that the seal is retaining or excluding, but also any contaminants (such as cleaning fluids or bi-products of reactions between any of these fluids, the seal material or the surrounding hardware).
Even a seemingly straightforward application can often involve a long list of chemicals and compatibility must be checked with the elastomer. Most seal suppliers publish compatibility tables or like us, have interactive tools to help check this. Even then, it’s often not the brand name oil that’s listed for example, but rather at the more basic chemical level, so some knowledge of what is actually in the fluid is required. Whilst recent developments in health, safety and environmental requirements have made this a little easier, some fluid manufacturers can still be a little reluctant to declare the full list of chemicals in their products.
They can sometimes give guidance on general compatibility with elastomer groups but this can be a little generic, and not all grades in a specific group will have the same resistance to a particular fluid. Again, this can be especially relevant to NBRs and HNBRs with a variable ACN content. Sometimes the reactions can be dramatic and swift, with the rubber shrinking or swelling in a matter of hours when exposed to a non-compatible fluid and especially at elevated temperatures where the chemical reaction is accelerated.
In other cases the reaction could be slower, but still causes sealing issues resulting in earlier system failure compared to using more capable elastomers. This is often the case with FFKM seals in applications where the cost of replacement or downtime is very high; the outstanding chemical resistance of these materials gives considerably longer service life compared to lesser grades, and it justifies the higher initial cost of the seal. In other cases some reactions can be beneficial, for example where a small amount of elastomer seal swell in an oil over time can help to offset wear in dynamic O-ring energized PTFE slipper seals.
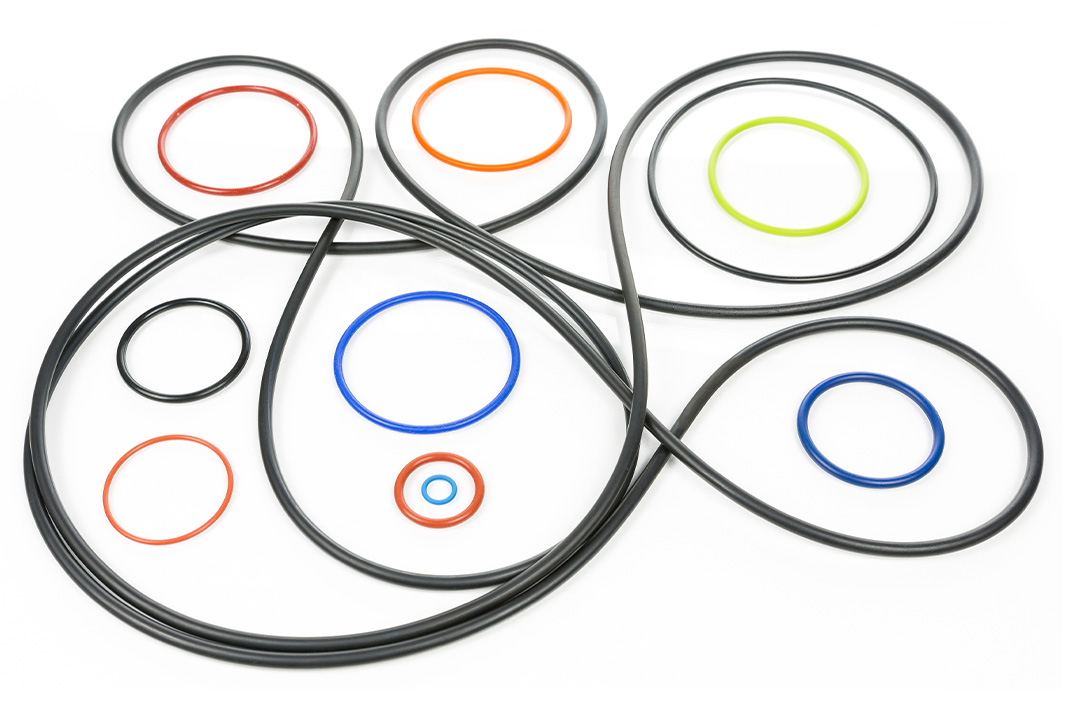
Temperature range
Outwardly, this material property seems straightforward, but elastomer technology is rarely that cooperative. All elastomer compounds will have a low temperature property stated on their datasheet, either the TR10 (temperature at which a stretched and frozen sample recovers by 10% of its length) or the Tg (the glass transition temperature, at which all flexibility is fully lost).
However, applied pressure increases the Tg by approximately 1°C for every 5 MPa, which can be significant for even moderately high pressure applications. Additionally, the flexibility required for successful sealing will vary between applications, making the correct material selection critical. At the other end of the spectrum, elastomers respond poorly when exposed to temperatures above their capability, and the material suffers irreversible degradation that reduces seal performance.
Whilst guidance can be given on maximum temperature capability for any specific elastomer grade, this is often in a benign air environment, so the chemical impact of being exposed to hot fluids in the sealing application should be considered.
Material groups tend to have well published temperature ranges. For example, the silicone family is able to reach -100°C (or even lower with special grades), and perfluoroelastomer (FFKM) grades are able to withstand 320°C (or even higher for short durations).
Confusingly though, considerable variations can exist even within the same material families; especially with FKM where the more modern grades can now reach down to -50°C, with older technology grades only capable of -15°C. There are many NBR and HNBR grades where the acrylonitrile (ACN) content can be varied so that the low temperature limits can be between -30°C and -60°C, depending on the specific recipe formulation.
This is just a short summary of three properties of elastomer materials. It’s clear that selecting the correct grade of material for a specific application is a difficult task, yet one that is absolutely critical to achieving the seal performance and lifetime required.