The importance of engineering tolerances
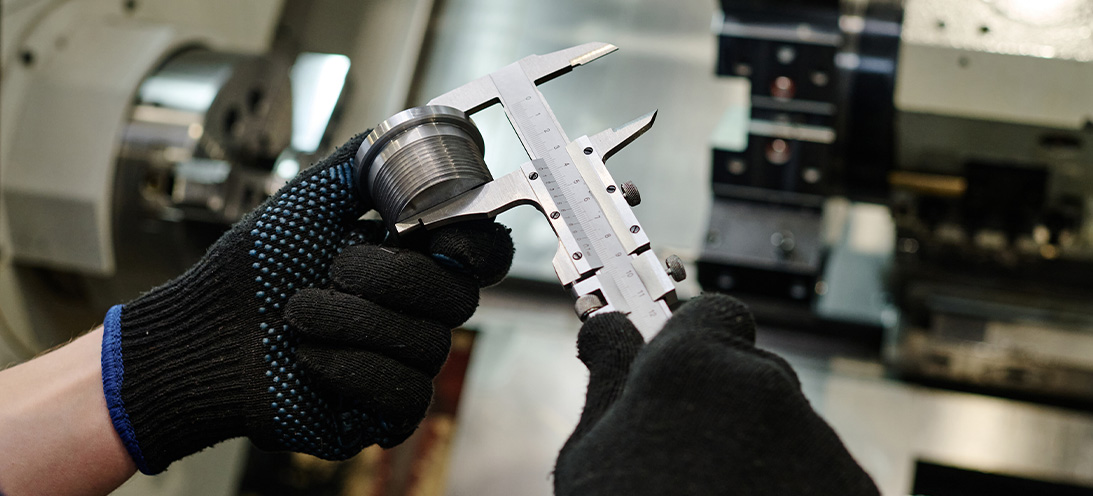
Tolerances are present in every man-made item. It is practically impossible to repeatedly manufacture something to an exact size or specification. In seal manufacturing, it’s important to understand which tolerances impact performance and by how much. This will ensure a system is optimized for overall performance, and whole-life product cost.
Considerations for tolerances include the seal material and the hardware for sealing installation.
Seal material, polymer and metal seals
Almost all polymer seal materials contain multiple ingredients. For PTFE and polyurethanes this is typically 2 or 3 different elements. Additionally, for an elastomer material, as many as 30 different ingredients can be used in the recipe.
In machined seals, polymer seal materials tend to have high rates of thermal expansion. Together with their relative softness, this makes it difficult to maintain the same level of tolerance that can be achieved when machining metal components.
Hardware tolerances
When designing hardware for seal installation, engineering tolerances are sometimes more obvious, and certainly where engineers can focus some attention.
A stack-up of tolerances for many applications should be considered. Together with tolerances of the assembly such as concentricity or misalignment (especially for dynamic sealing applications). Other considerations include bearing wear and the resulting increase in misalignment or runout as the equipment approaches the end of it’s target life.
Why are engineering tolerances important for sealing systems?
Every application starts from a nominal condition, and the maximum and minimum tolerance conditions should always be considered. Even in seemingly straightforward applications, it’s important to ensure the seal is continuing to operate within it’s ideal set of conditions.
Click on the link for information about our engineering, design and innovation service, click on this link HERE
Use our interactive tools HERE
What tolerances are we concerned with?
We can start with the seal itself, and specifically the seal material, as almost all polymer seal materials contain multiple ingredients. For PTFE and polyurethanes this is typically 2 or 3 different elements, but for an elastomer material as many as 30 different ingredients can be used in the recipe. Each ingredient is weighed or measured before being added to the mixing machine, with a tolerance on the mass or volume of the solid or liquid ingredient.
Digital advances in weighing and dosing equipment have improved tolerance ranges since synthetic rubbers were first commercially produced in the 1930’s, but a small variation in material mix from batch to batch is inevitable.
The mixing process (also now digitised to help reduce variation) is controlled by parameters which also have a tolerance. Pressures, temperatures, speeds and times will be kept within certain limits and determined by the sophistication of the mixer and it’s control systems.
For the production of the finished seal, mould tools for polyurethane and elastomer seals can be manufactured using CNC or electrical discharge machining techniques. These hold incredibly tight tolerances on the metal form, but variations in moulding pressure and temperature combined with slight variations in material shrinkage rates will give tolerances on the finished parts that are significantly wider than the metal tool it was produced from. For machined seals, polymer seal materials tend to have high rates of thermal expansion. This together with their relative softness makes it difficult to maintain the same level of tolerance that can be achieved when machining metal components.
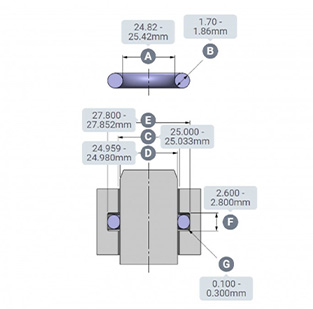
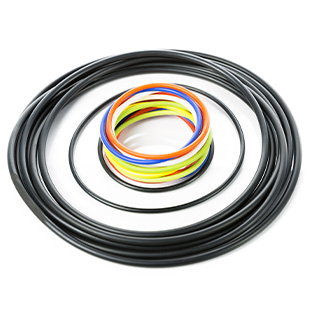
Hardware tolerances
When designing hardware for seal installation, this is where the tolerances are perhaps more obvious, and certainly where engineers can focus some attention. Plastic housings (whether injection moulded or machined) together with metal castings or pressings can pose tolerance challenges; but even for relatively straightforward machined metal housings selecting the correct tolerance to apply is key.
For many applications a stack-up of tolerances should be considered, along with tolerances of the assembly such as concentricity or misalignment (especially for dynamic sealing applications). Other considerations include bearing wear and the resulting increase in misalignment or runout as the equipment approaches the end of it’s target life.
Why are tolerances important for sealing systems?
Through a combination of theory and experience over decades, seal designers have developed an ideal set of installation conditions for many applications; from static flange or face sealing, through linear hydraulic cylinder seals and to rotary shaft sealing and more. Some of these applications have adopted standardised recommendations (such as ISO 3601 for o-rings and DIN 3760 for elastomer shaft seals) but since no two applications are truly identical many are based on the experience and preferences of the seal designer.
Regardless, every application starts from a nominal condition, and the maximum and minimum tolerance conditions should always be considered even in seemingly straightforward applications to ensure the seal is continuing to operate within it’s ideal set of conditions.
Sometimes it’s assumed that tolerances only really come into play when looking at very small applications, with so-called “micro O-rings”, but this is not the case. We can illustrate this with a hypothetical application:
A device containing a 25 mm rod, static, with an FKM O-ring sealing gas, whilst installed for 10 years untouched in the Arctic circle. However, it also needs to seal oil whilst installed in direct sun at the equator for 10 years, but with the rod removed and re-fitted several times a year. The device designer would prefer not to make two different variants.
O-ring calculators working to ISO 3601 would recommend a 25.12 mm x 1. 78 mm O-ring fitted in a 27.8mm groove with f7 tolerance on the rod and H9 on the groove. However, in the cold application the worst case squeeze is looking a little light to ensure long term gas sealing whilst in the high temperature location, the compression and groove fill are reaching levels that could accelerate compression set of the material and cause issues when the rod is disturbed and re-fitted.
Moving the nominal sizes would help one installation, but adversely impact the other; but by tightening the tolerance on the rod and the groove the concerns at the extreme conditions can be lessened. Approaching the seal supplier for tighter tolerance O-rings can improve the robustness of the design even further, as could incorporating a custom bonded seal-rod component which would remove one dimension and it’s tolerance completely. Such a hypothetical application rarely exists of course, but the approach is applicable to a surprisingly large number of applications which appear “standard” at first glance.
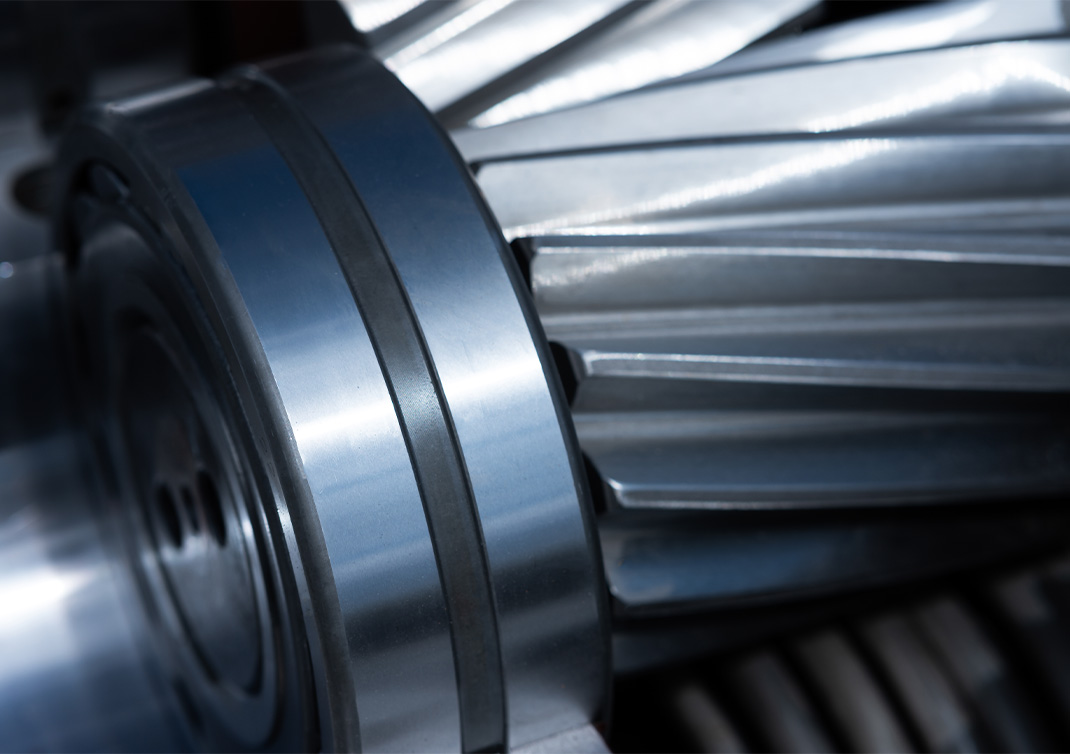
What hardware tolerances should be specified?
There is not a definitive answer to this question, but more of a recommendation that the tolerances for each component within an application are considered – with both the technical and financial impacts being evaluated. Sometimes applying a tighter tolerance can be achieved without any cost implications, but in other cases it might slow the manufacturing process, or potentially require a different and more costly process (for example, grinding a rod in place of turning).
Tolerances should be evaluated by the consequences of the complete sealing system not performing as intended at the absolute extremes of potential tolerance conditions. In applications where the impact of non-optimal performance may be less severe, a paper based or theoretical tolerance evaluation could provide enough confidence that the risk and impact of the problem arising is acceptable compared to the costs of preventing the risk further.
In some safety critical applications in Life Sciences & Medical, Aerospace or Vehicle Control systems markets, testing of parts at the most extreme sizes may be required to be certain that any combination of components from anywhere within their minimum or maximum range of tolerance sizes would still produce an assembly product which performs successfully in the application.