Seals for Life Sciences & Medical Applications
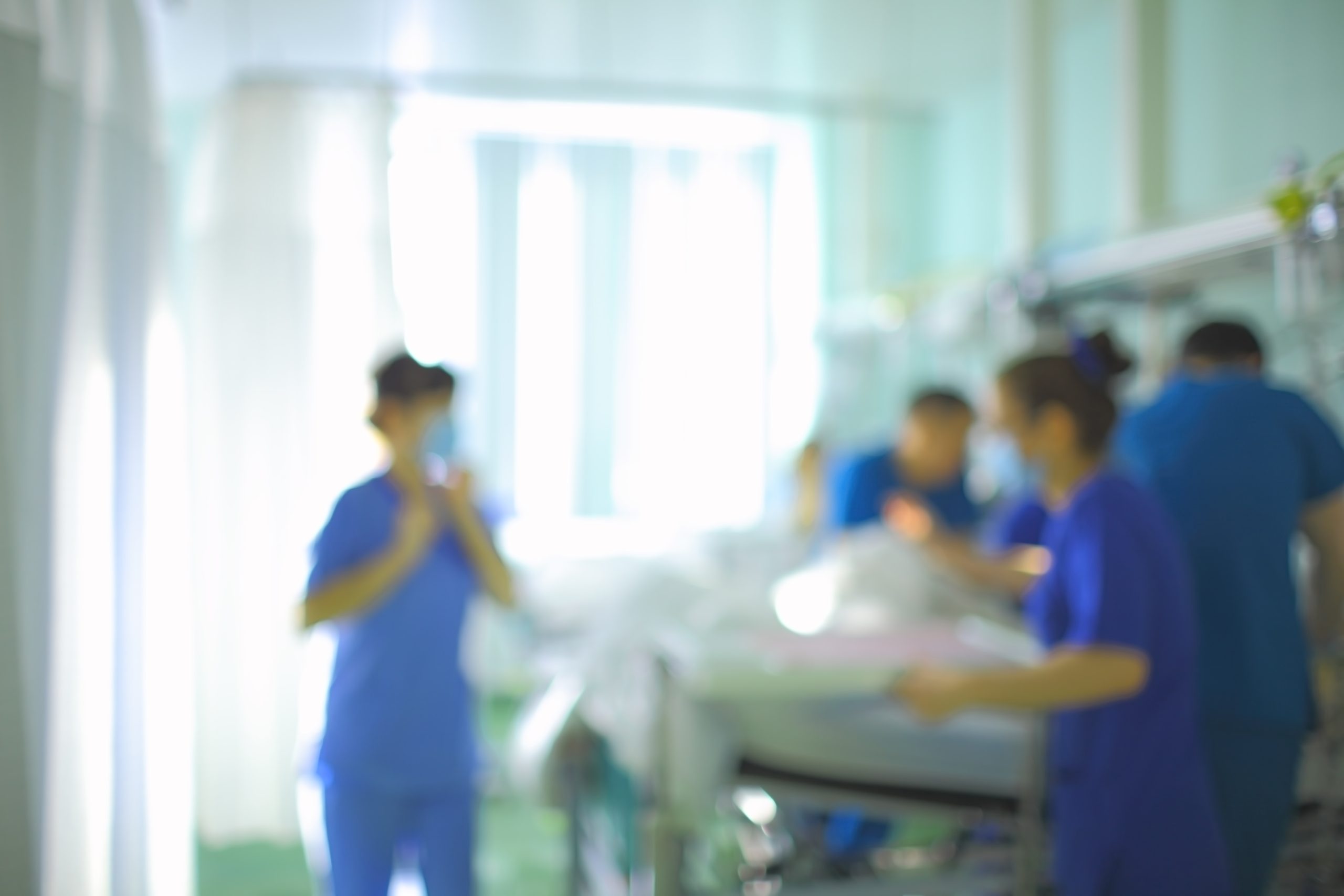
When designing and manufacturing sealing solutions for applications within critical devices and equipment, the strictest demands in product integrity and the highest specifications of hygiene and cleanliness must be met.
Characteristics of Life Sciences & Medical sealing
The Life Sciences & Medical industry is one of the most demanding and stringently regulated. There are a variety of areas of product development and manufacture where seals for Life Sciences & Medical Applications are required.
Diagnostics
Because of technology changes, there are now many ways of supporting patients with accurate results for the safe management of health conditions. This includes at home and within a clinical setting. It’s vital that diagnostic devices and systems are developed with the accuracy and speed of response to enable targeted analysis and therapy.
Patient management and care
Repeatable and reliable control of the equipment used in patient management and care is paramount. Applications include seals for ventilators, anaesthesia pumps, respiratory therapy and monitoring equipment. Minimally invasive surgery equipment and metered dose aerosols (such as inhalers) also need Life Sciences & Medical seals. Optimised working friction and wear life are demands on seals. The critical feature’s function & tolerance control are also pressures on the seal, coupled with management of gas, liquids, or solid media at accurate rates.
Biotech and pharmaceutical processing
There’s continued development of complex and expensive drugs and research control media. Therefore, demand for high performance interactive components within the biotechnology process industry is crucial. Typical applications include seals for analytical equipment, pumps, valves & actuators, monitoring & control equipment. In addition to storage equipment & transportation vessels. We support engineers on recommending Ultra High Purity (UHP) materials for application working extremes correspondingly with sensitive chemical media, and seal design recommendations for dead space and entrapment elimination within these applications.
Ultra High Purity (UHP) materials
Silicone based rubbers are a common choice of elastomer materials for seals used within medical devices. This is because of their biocompatibility features and resistance to bacterial growth. Commonly they’re platinum cured for injection moulded liquid silicone rubbers (LSR’s) and platinum and peroxide cured for compression moulded heat cured silicones (HCR’s). There’s a diverse range of silicone rubbers currently available in varying shore hardness’s that are already approved, making them a go to choice if the specification allows.
An application could need a seal material to have better mechanical properties or more temperature versatility or media compatibility. Therefore EPDM and FKM rubbers are also a good choice.
Many of our materials are fully compliant and therefore have the required industry approvals, read more HERE
Cleanroom Manufacturing
Life Science and Medical sealing products are produced in a cleanroom environment. Especially this is essential for manufacturing and packaging of products. Equally, external particulates such as dust, dirt, airborne microbes, and aerosol particles should not come into contact or contaminate the surface/the area.
A cleanroom is created by removing air, circulating through a filtering system and distributing (the filtered) back into the cleanroom. This is achieved at varying levels of cleanliness depending on what is specified for each individual manufacturing environment, or the finished product requirements.
Different cleanliness levels are classified by the concentration of airborne particles within a measured space. We provide a complete cleanroom production process. This includes material blank production through to inspection and packaging using controlled materials within state-of-the-art cleanrooms.
Read more about our Life Sciences & Medical industry expertise HERE
Characteristics of Life Sciences & Medical sealing
The Life Sciences & Medical industry is one of the most demanding and stringently regulated. There are a variety of areas of product development and manufacture where sealing solutions are required.
Diagnostics
Technology changes over recent years mean there are now many ways of supporting patients with accurate results for the safe management of health conditions; both at home and within a clinical setting. Either way, it’s vital that diagnostic devices and systems are developed with the accuracy and speed of response to enable targeted analysis and therapy. Typical applications include seals for in-vitro devices, analytical laboratory equipment, x-ray, and CT/MRI scanning equipment. We support your engineers with efficient design and project management of optimised sealing components for both clinical and patient self-diagnosis.
Patient management and care
For obvious reasons, repeatable and reliable control of the equipment used in patient management and care is paramount. Typical applications include seals for ventilators, anaesthesia pumps, respiratory therapy, monitoring equipment, minimally invasive surgery equipment and metered dose aerosols (such as inhalers). The typical demands on these types of seals include optimised working friction and wear life, critical feature’s function & tolerance control, and the management of gas, liquids, or solid media at accurate rates.
Biotech and pharmaceutical processing
Due to the continued development of complex and expensive drugs and research control media, the demand for high performance interactive components within the biotechnology process industry is crucial. Typical applications include seals for analytical equipment, pumps, valves & actuators, monitoring & control equipment and storage equipment & transportation vessels. We support engineers on recommendations Ultra High Purity (UHP) materials for application working extremes combined with sensitive chemical media, and seal design recommendations for dead space and entrapment elimination within these applications.
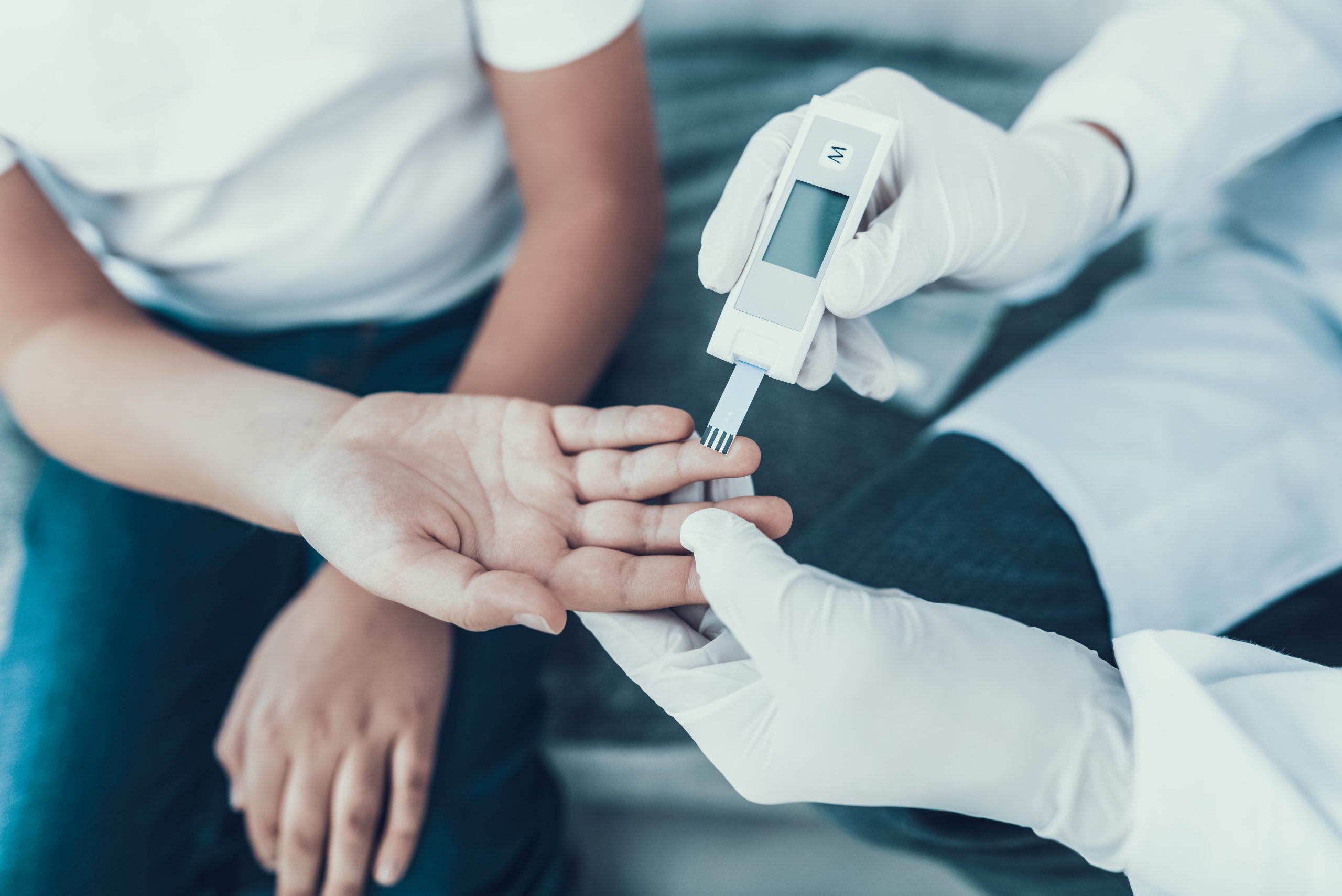
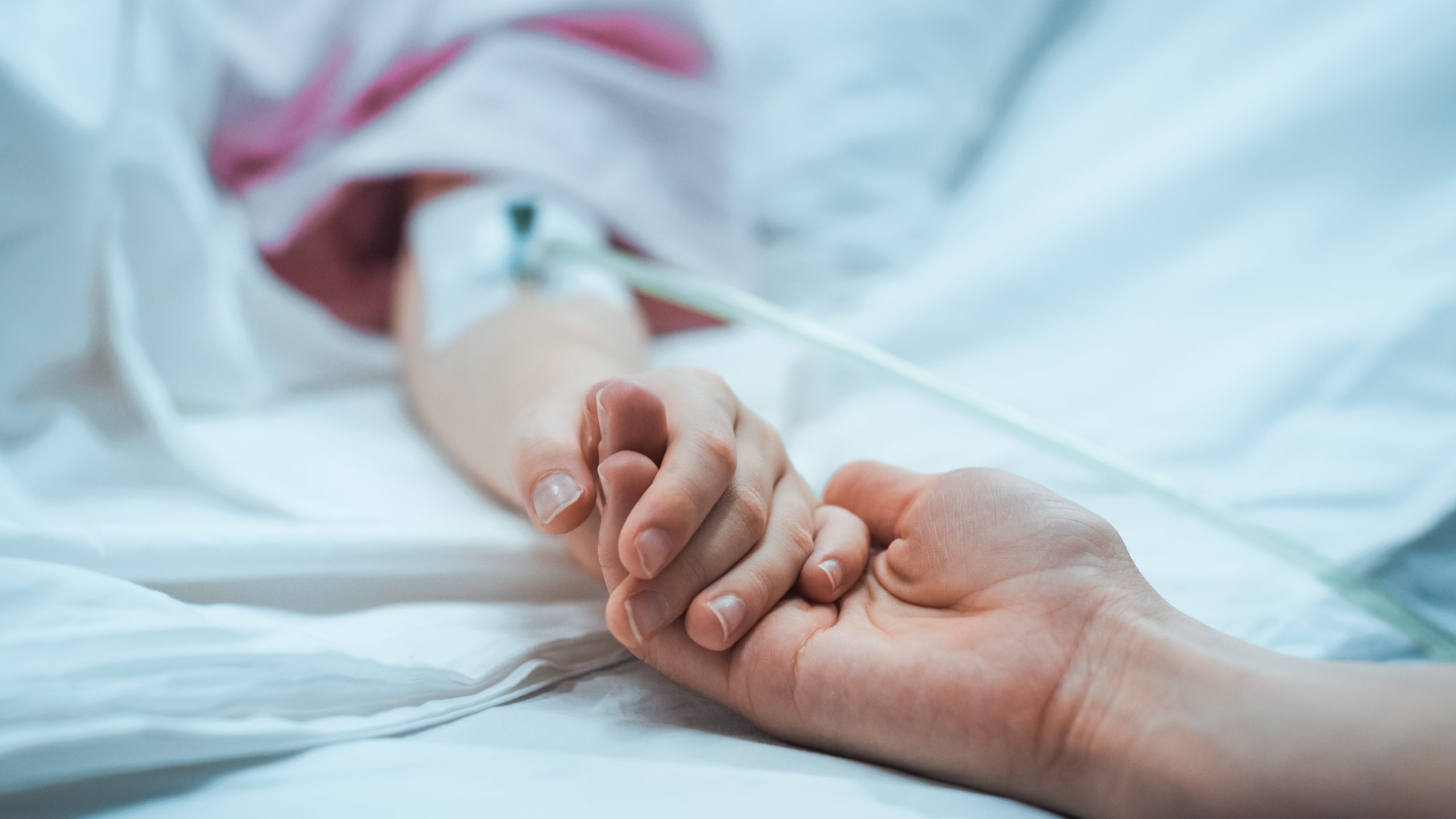
Ultra High Purity (UHP) materials
Silicone based rubbers are a common choice of elastomer materials for seals used within medical devices due to their biocompatibility features and resistance to bacterial growth. Commonly they’re platinum cured for injection moulded liquid silicone rubbers (LSR’s) and platinum and peroxide cured for compression moulded heat cured silicones (HCR’s). There’s a diverse range of silicone rubbers currently available in varying shore hardness’s that are already USP Class VI or ISO 10993 approved, making them a go to choice if the specification allows.
If an application calls for a seal material to have better mechanical properties or more versatility with temperature range or media compatibility then EPDM and FKM rubbers are also a good choice.
Many of our materials are fully compliant and have the required industry approvals, such as with FDA, USP Class VI, ISO 10993, UHP, BAM and BfR standards.
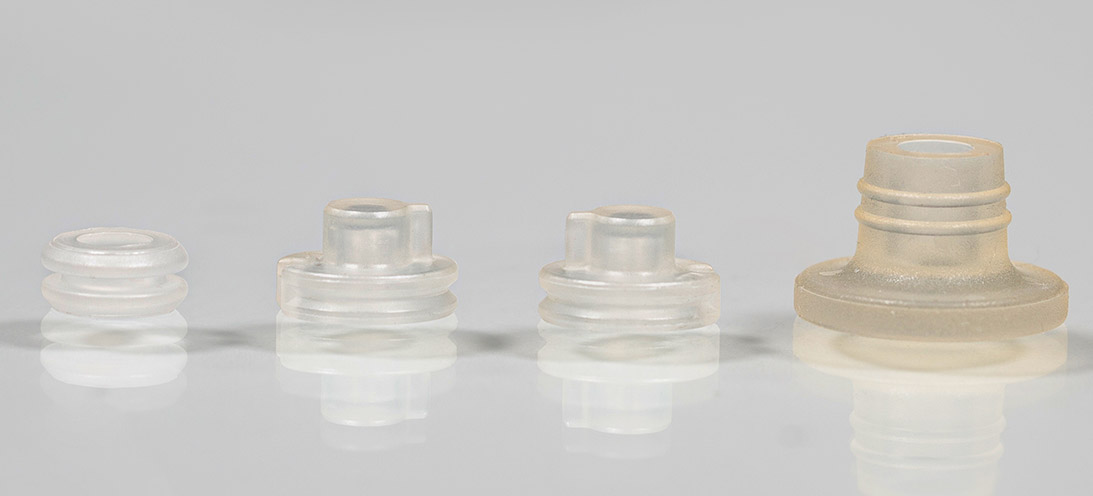
Cleanroom Manufacturing
A controlled cleanroom environment is essential for manufacturing and packaging of products that must have no contact or contamination from external particulates such as dust, dirt, airborne microbes, and aerosol particles.
It is created and maintained by removing the air, circulating it through a filtering system and distributing (the clean and filtered) air back into the cleanroom environment. This can be achieved at varying levels of cleanliness, and it depends on what is specified for each individual manufacturing environment or the finished product requirements.
Different cleanliness levels are classified by the concentration of airborne particles within a measured space. We provide a complete cleanroom production process; from material blank production through to inspection and packaging using controlled materials within state-of-the-art cleanrooms.