Seals for Oil & Gas applications
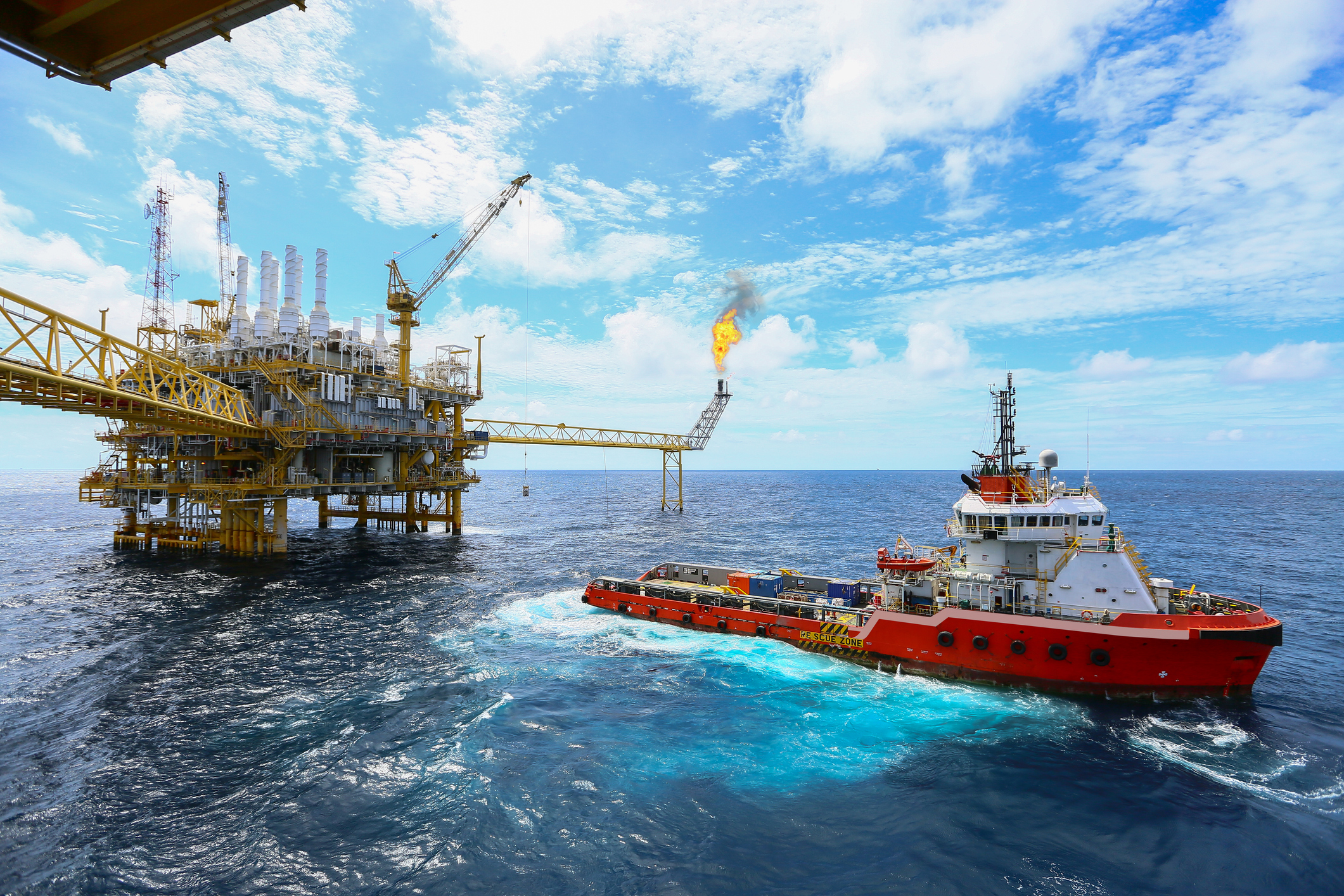
With diverse applications in harsh environments, the Oil & Gas industry presents some of the most challenging demands on engineered sealing solutions. Our collaboration with Parker Seal Group allows us to integrate their materials and sealing expertise to meet our customer demands.
Characteristics of Oil & Gas sealing
Regardless of where seals are used in oil & gas applications, they are without doubt critical to the safe, reliable and efficient operation of a huge range of onshore and offshore equipment. There are many challenges involved in oil & gas application sealing; conditions typically include low and high temperature extremes, very high pressure conditions and most seals need to withstand aggressive fluids and media such as sour gas, salt water and super-heated steam.
There are three main sectors within the Oil & Gas industry, with different processes and equipment requiring sealing solutions. Upstream; commonly known as exploration and production – this refers to the recovery of hydrocarbon reserves in the form of natural gas and crude oil. Midstream; refers to the processes involved in the transportation and storage of natural gas and crude oil, from production site to refinery location. Downstream; includes the processing of natural gas and crude oil at oil plants and petrochemical plants.
Well Drilling
This is the process of extracting oil and gas from beneath the ground, in both onshore and offshore environments. Seals used in these applications have to cope with increasingly harsh environments (with wells becoming deeper and deeper). System pressures up to 30,000 PSI and operating temperatures between -50°C and +220°C are common, and seals have to demonstrate excellent fluid compatibility and resistance against aggressive media – all with longer service life expectations.
Applications include; drilling and tool bits, blow-out preventers, drilling mud systems, LWD and MWD test equipment, casing and pipe connections, subsea risers and connector systems, control valves, compressors and pumps.
Seals need; high temperature and high pressure capabilities, sour gas and abrasive drilling fluids resistance, extrusion resistance and compatibility with well bore fluids.
Well Completion
This is the process of making a well ready for production after drilling. Similiar to well drilling, seals used in well completion must withstand increasingly harsh condition such as deeper wells and more diverse geographical areas with extreme hot and cold weather conditions. System pressures up to 30,000 PSI and operating temperatures between -45°C and +220°C are common, and seals have to demonstrate excellent fluid compatibility and resistance against aggressive media.
Applications include; tubing heads and hangars, packer assemblies, well controls, Christmas trees, cementing equipment, well head completion assemblies, well service.
Seals need; high temperature and high pressure capabilities, chemical compatibility (including H2S resistance), RGD & extrusion resistance and steam resistance.
Distribution
Following on from the production stage, petroleum products are transported to processing facilities and to end users in pipelines. Seals used in midstream distribution sector applications often operate in low temperatures, down to -196°C (required to liquify gas) as well as high temperatures of 480°C (to meet fire test requirements). System pressures can be as high as 10,000 PSI.
Applications include; marine and offshore loading swivels and turrets, railcar loading systems, pipeline service equipment (pigs and spheres), pipeline valves & actuators, pumps & compressors, tank & loading systems.
Seals need; Extrusion, corrosion and abrasion resistance, extreme temperature and pressure capabilities, chemical compatibility (including H2S), RGD resistance, compliance with NORSOK, ISO and API specifications.
API 6A, NORSOK M-710, ISO 23936-2 and TOTAL material qualifications
The Oil & Gas industry has specific testing and qualification standards to ensure that materials used in harsh drilling and production environments meet the critical demands of these applications.
ISO 23936-2:2011 describes the requirements and procedures for the qualification of elastomeric materials in accordance with media related to oil and gas production. H2S testing in accordance with this specification enables the lifetime prediction of compounds.
NORSOK M-710 defines the requirements for critical non-metallic (polymer) sealing, seat and anti-extrusion ring materials for permanent subsea use. This includes well completion, christmas trees, control systems and valves as well as topside valves in critical gas systems.
API 6A is the specification for drilling and production, wellhead and christmas tree equipment.
Total GS EP PVV142 defines the requirements for non-metallic sealing materials concerning elastomers within pipeline valve applications.
In conjunction with Parker Seals we offer a range of products in materials that are qualified to these specifications.
We work closely with our oil & gas customers, read more HERE
Characteristics of Oil & Gas sealing
Regardless of where seals are used in oil & gas applications, they are without doubt critical to the safe, reliable and efficient operation of a huge range of onshore and offshore equipment. There are many challenges involved in oil & gas application sealing; conditions typically include low and high temperature extremes, very high pressure conditions and most seals need to withstand aggressive fluids and media such as sour gas, salt water and super-heated steam.
There are three main sectors within the Oil & Gas industry, with different processes and equipment requiring sealing solutions. Upstream; commonly known as exploration and production – this refers to the recovery of hydrocarbon reserves in the form of natural gas and crude oil. Midstream; refers to the processes involved in the transportation and storage of natural gas and crude oil, from production site to refinery location. Downstream; includes the processing of natural gas and crude oil at oil plants and petrochemical plants.
Well Drilling
This is the process of extracting oil and gas from beneath the ground, in both onshore and offshore environments. Seals used in these applications have to cope with increasingly harsh environments (with wells becoming deeper and deeper). System pressures up to 30,000 PSI and operating temperatures between -50°C and +220°C are common, and seals have to demonstrate excellent fluid compatibility and resistance against aggressive media – all with longer service life expectations.
Applications include; drilling and tool bits, blow-out preventers, drilling mud systems, LWD and MWD test equipment, casing and pipe connections, subsea risers and connector systems, control valves, compressors and pumps.
Seals need; high temperature and high pressure capabilities, sour gas and abrasive drilling fluids resistance, extrusion resistance and compatibility with well bore fluids.
Well Completion
This is the process of making a well ready for production after drilling. Similiar to well drilling, seals used in well completion must withstand increasingly harsh condition such as deeper wells and more diverse geographical areas with extreme hot and cold weather conditions. System pressures up to 30,000 PSI and operating temperatures between -45°C and +220°C are common, and seals have to demonstrate excellent fluid compatibility and resistance against aggressive media.
Applications include; tubing heads and hangars, packer assemblies, well controls, Christmas trees, cementing equipment, well head completion assemblies, well service.
Seals need; high temperature and high pressure capabilities, chemical compatibility (including H2S resistance), RGD & extrusion resistance and steam resistance.
Distribution
Following on from the production stage, petroleum products are transported to processing facilities and to end users in pipelines. Seals used in midstream distribution sector applications often operate in low temperatures, down to -196°C (required to liquify gas) as well as high temperatures of 480°C (to meet fire test requirements). System pressures can be as high as 10,000 PSI.
Applications include; marine and offshore loading swivels and turrets, railcar loading systems, pipeline service equipment (pigs and spheres), pipeline valves & actuators, pumps & compressors, tank & loading systems.
Seals need; Extrusion, corrosion and abrasion resistance, extreme temperature and pressure capabilities, chemical compatibility (including H2S), RGD resistance, compliance with NORSOK, ISO and API specifications.
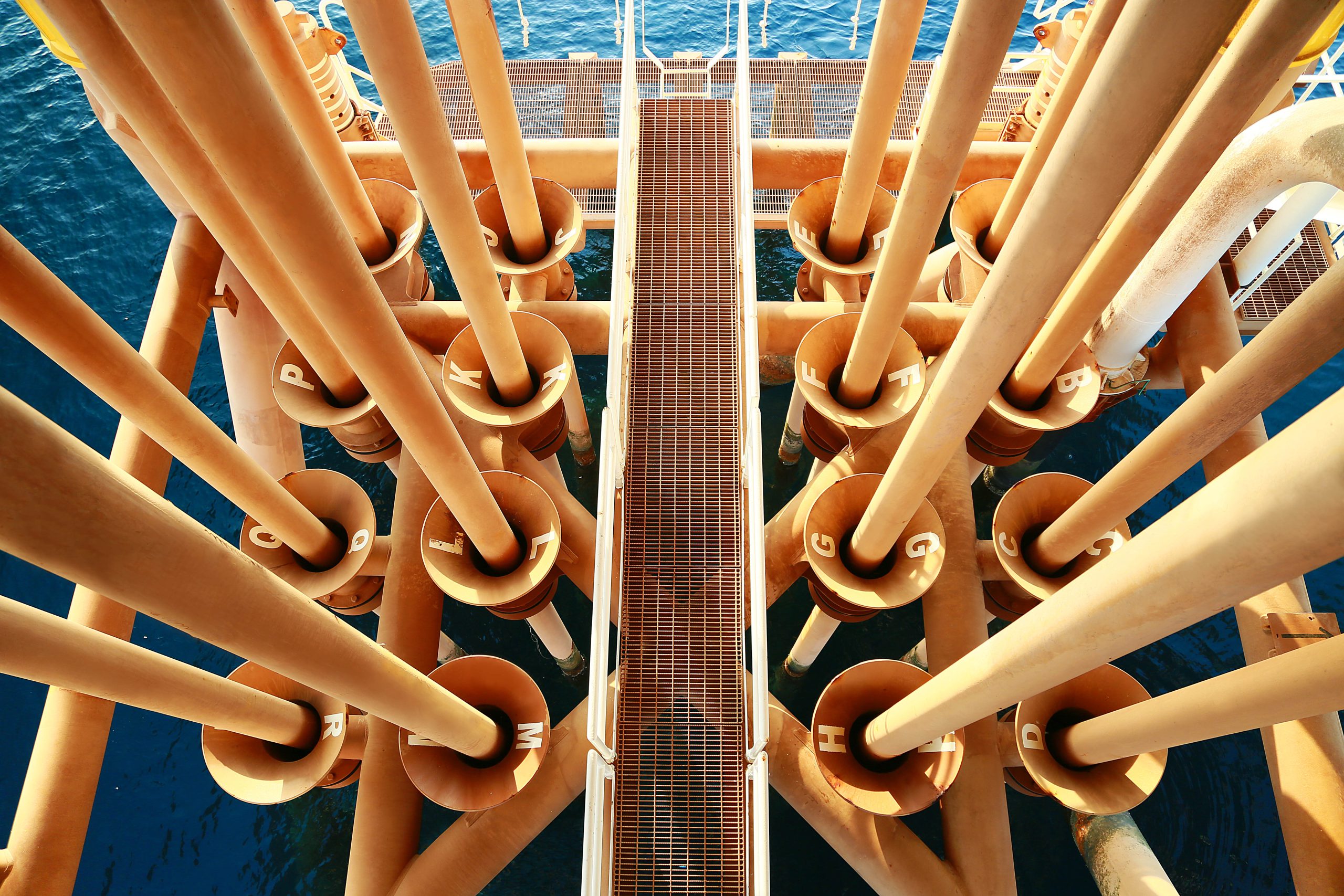
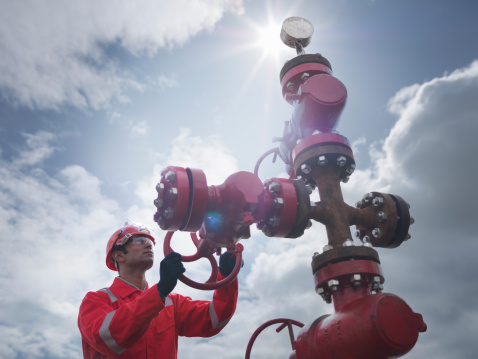
API 6A, NORSOK M-710, ISO 23936-2 and TOTAL material qualifications
The Oil & Gas industry has specific testing and qualification standards to ensure that materials used in harsh drilling and production environments meet the critical demands of these applications.
ISO 23936-2:2011 describes the requirements and procedures for the qualification of elastomeric materials in accordance with media related to oil and gas production. H2S testing in accordance with this specification enables the lifetime prediction of compounds.
NORSOK M-710 defines the requirements for critical non-metallic (polymer) sealing, seat and anti-extrusion ring materials for permanent subsea use. This includes well completion, christmas trees, control systems and valves as well as topside valves in critical gas systems.
API 6A is the specification for drilling and production, wellhead and christmas tree equipment.
Total GS EP PVV142 defines the requirements for non-metallic sealing materials concerning elastomers within pipeline valve applications.
In conjunction with Parker Seals we offer a range of products in materials that are qualified to these specifications.
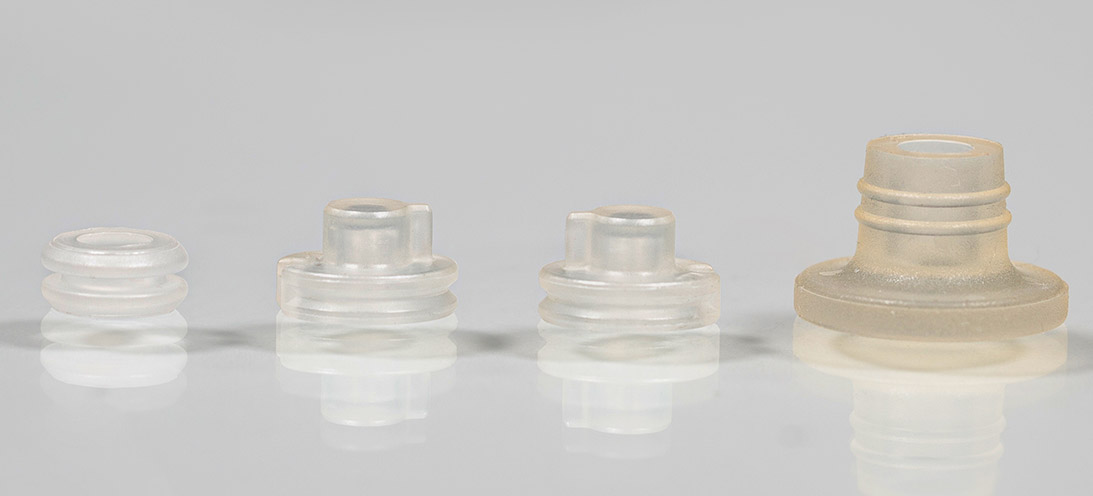