High speed Rotary seals for electric vehicles
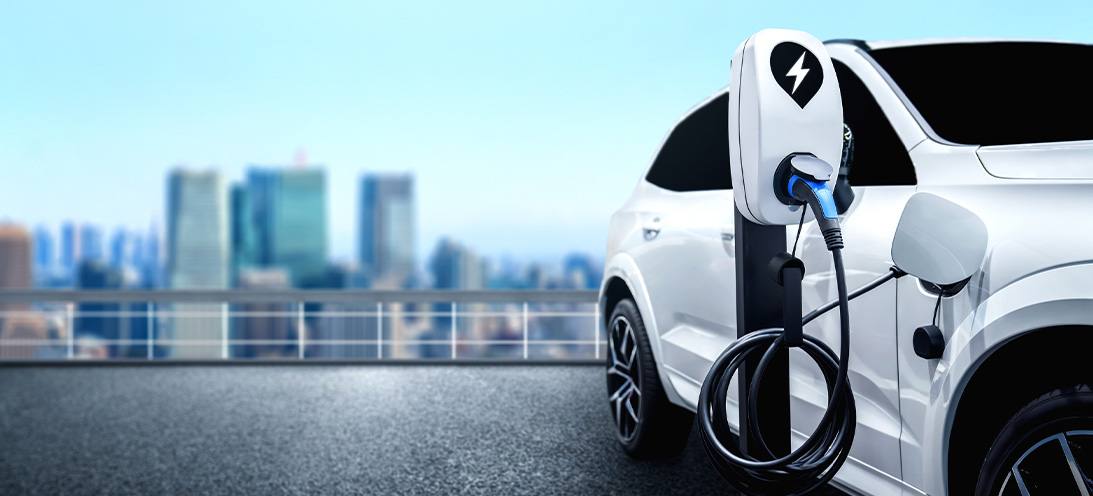
The application
With over 30 years’ experience of providing pioneering technologies globally to the mobility industry, this established customer is a supplier of powertrain solutions for electric and hybrid vehicles, as well as traditional internal combustion power engines.
This team of powertrain development experts approached our engineers for a rotary shaft sealing solution for the gearbox within an electric vehicle. The position of the seal was required between the wet transmission and dry e-motor, and pressed into a bulkhead housing.
The sealing lip runs on the surface of the transmission rotor shaft and pressed radially by a tension spring onto the shaft, and required a dust lip to provide protection against dirt and debris from the environment on the dry motor side.
The shaft and housing dimensions were all fixed by the customer, but they provided a full dimensional, surface finish, pressure, temperature and media specification for our engineers to review and propose a bespoke seal design.
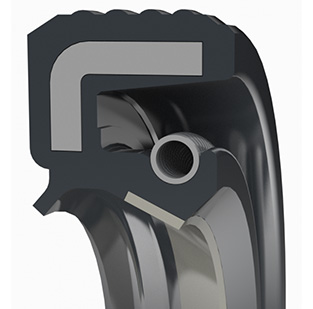
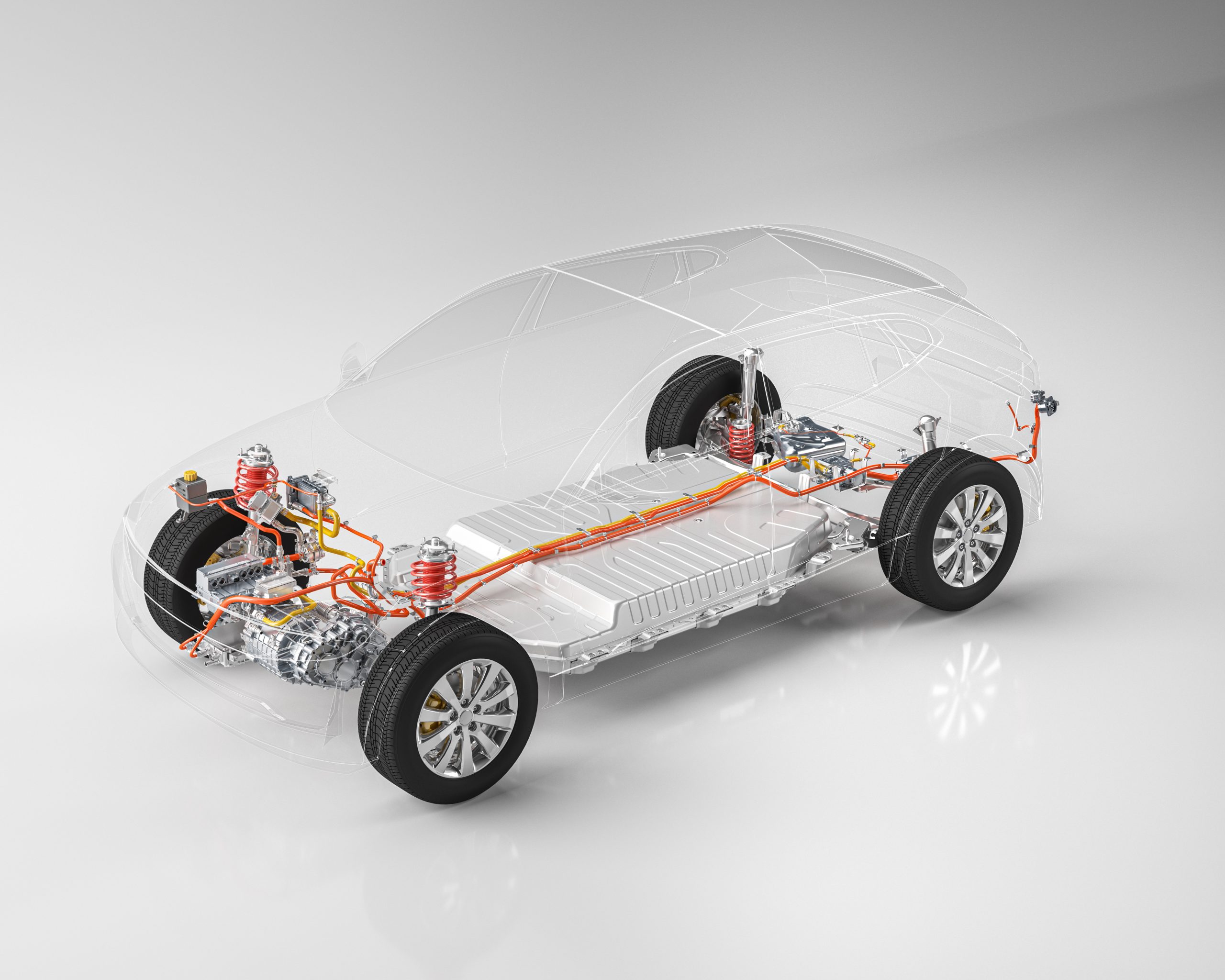
Our sealing solution
The application media was a synthetic oil; relatively standard for an automotive application, but because of the maximum working temperature, FKM (Viton) was the elastomer material to meet the required range.
As with many applications within electric vehicle gearboxes, the shaft speed was particularly high at 8500 RPM. Typically with these high speeds, seal design needs to ensure minimal friction to ensure the service life required.
Our application engineers designed a bespoke, double lipped spring energised seal.
On the dry e-motor side, the rubber lip was designed to act as a dirt and dust excluder, with slight clearance from the shaft to avoid friction which prevented damage to the seal and also unnecessary wear to the rotary system as a whole.
In the wet transmission side it was imperative that the oil was kept away from the e-motor with the same minimal friction requirements. As a result, our engineers designed the seal with an inlaid PTFE lip with 15% graphite fill. It was energised with spring to ensure force to achieve ultimate shaft sealing performance.