PolyTetraFluoroEthylene & TFM
PolyTetraFluoroEthylene (PTFE) is a synthetic fluoropolymer of tetrafluoroethylene and contains just two elements; carbon and fluorine. TFM is a modified PTFE.
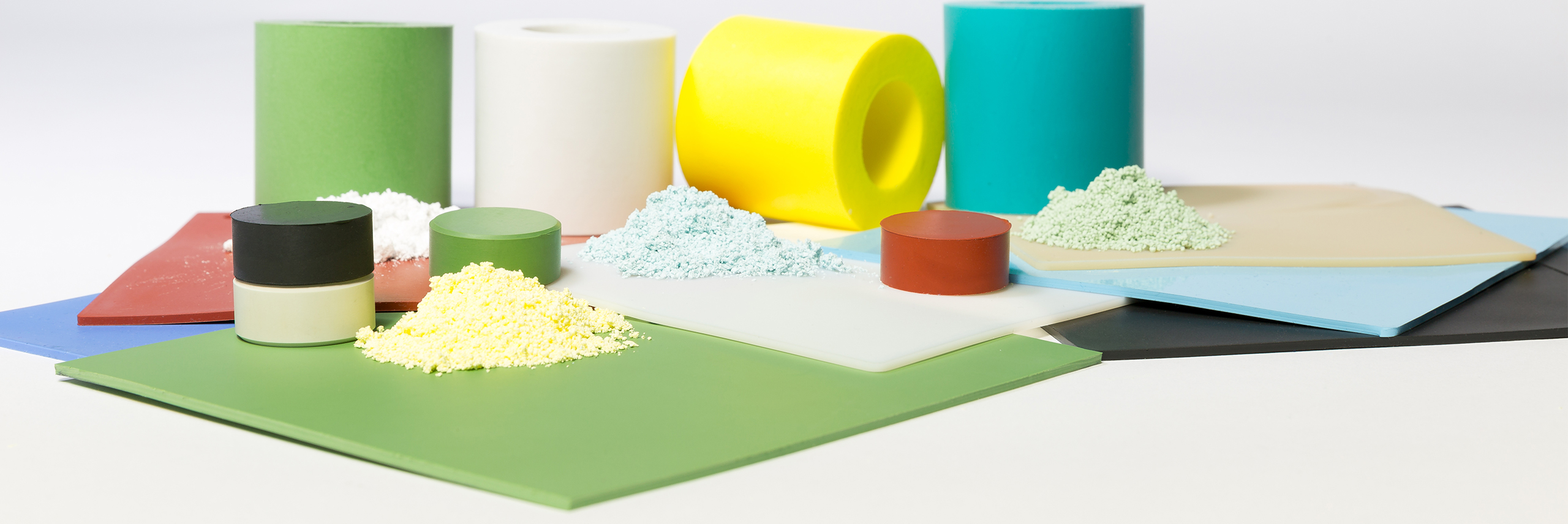
What is PTFE/TFM?
PTFE (PolyTetraFluoroEthylene) is a synthetic fluoropolymer of tetrafluoroethylene and contains just two elements; carbon and fluorine. A thermoplastic polymer of high molecular weight, it has one of the lowest friction coefficients of any solid and is virtually chemically inert due to the strength of the bonds between the fluorine and carbon atoms. Together with a high melting point, these properties combine to give a material that is ideally suited for use in sealing applications although due to low levels of elasticity, it is often necessary to combine a PTFE seal element with an energizer (either an elastomer or a metallic spring). TFM (modified PTFE) is copolymerized PTFE introducing an oxygen molecule and results in a higher density material with lower gas permeation, reduced cold flow and a smoother surface finish when machined.
When to use PTFE/TFM
PTFE seals exhibit much lower levels of friction compared to elastomer seals and the breakout friction is only marginally above the running value, thus virtually eliminating the stick-slip phenomenon associated with other sealing materials, even in applications that have poor or no lubrication. The material has a very broad operating temperature range, with the same compound being capable of cryogenic temperatures to over 300°C (572°F) whilst the near universal chemical resistance makes it ideal for use in chemically harsh environments or where the seals may be exposed to a variety of contaminants. A range of fibre and powder fillers can be added to the virgin PTFE to produce compounds with the optimum combination of wear and extrusion resistance to suit the application. The need to include some sort of energizer, coupled with the inability to injection mould PTFE for high volume applications, can result in seals using this material being relatively expensive compared to those using other sealing materials. However, the life and / or performance benefits achievable with PTFE seals can often result in a far more cost effective solution when full life costs are considered.
Wherever an application has a temperature or chemical resistance requirement that alternative sealing materials cannot accommodate, a PTFE based solution is the natural choice, and such applications can be found across a very wide variety of market fields, from space, to oil and gas, semiconductor manufacture, CPI, food, beverage and pharma amongst many others. Where an application relies on low, and consistent levels of friction, or demands a long endurance life, PTFE seals are ideal and can be matched to the application by detailed design of the seal and the energizer. Whilst fundamentally resistant to all chemicals (with the exception of alkali metals and rare fluorinating agents) it is broken down by prolonged exposure to ionizing radiation, such as Gamma rays and high intensity X Rays. Having an operating temperature range of -268°C (-450°F) to +315°C (600oF), special seal designs may be required below -100°C (-148°F) to compensate for thermal shrinkage of the material, whilst softening above +260°C (500°F) may require the seal to be supported against extrusion or deformation.
Standard PTFE/TFM materials
This is a small selection of our general purpose PTFE and TFM materials. Many more compounds are available and can be chosen to suit the specifics of the application.
The tensile strength and elongation are for specification purposes. Typical achieved values can be significantly higher.
Temperature range is general recommendation for static application in air. Temperature ratings are subject to full application review.
