O-rings with special coatings
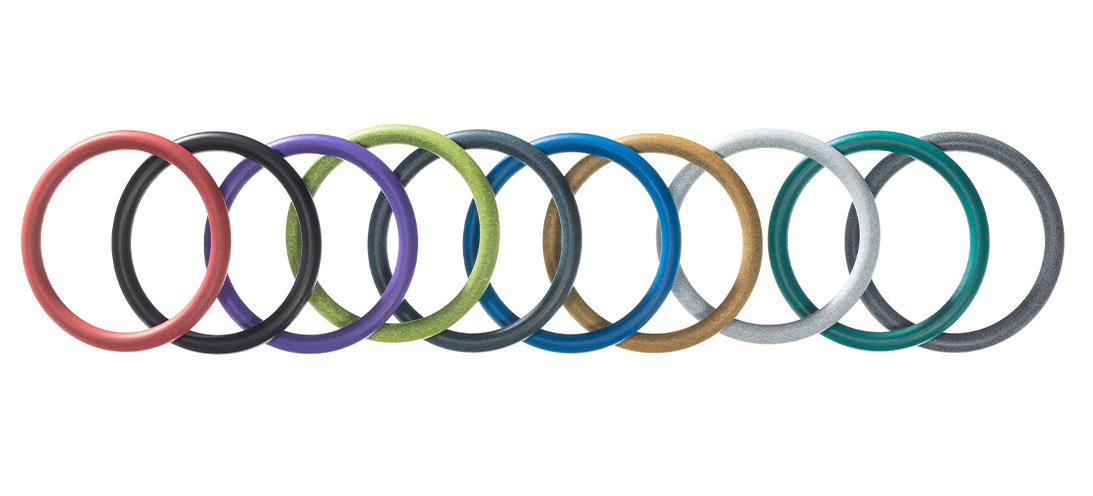
Why use special coatings for seals?
The main function of coatings is to improve installation into the hardware and to lower friction within an application; but there are many other benefits too. They often mean that lower assembly forces are required and by not using grease lubricants seal parts don’t stick together in packaging for transit. Special coatings can be manufactured in different colours so that seals and O-rings for specific applications can be easily identified without the need to reformulate the elastomer compound with colour additives. All of these reasons make them easier to handle for users during installation.
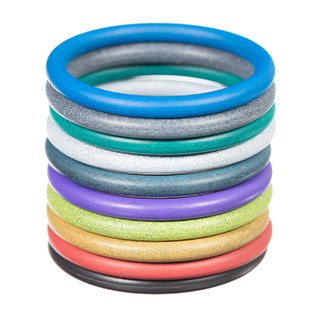
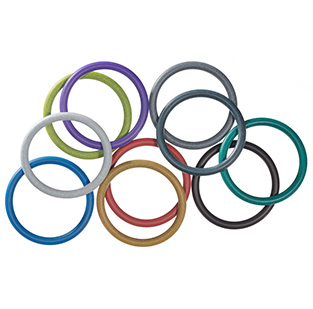
What types of coatings are there?
There are a variety of coatings and lubricants available for the surface area of seals, and they’re mainly divided into two common categories; wet coating/lubrication or dry micro film coating. Historically, coating technology was limited to just using wet type coatings. For example these may include silicone oils and greases and mineral oil based greases. The coating process would involve simply dipping the seals in the oil or grease during manufacture, or during installation on site. This is often be a messy process, and although a relatively low cost method, wet coating is less common as more applications demand higher levels of cleanliness and control of products, and low contamination has become a key factor.
Alongside the typical wet coatings traditionally used, there is an extensive range of what is often referred to as dry coatings. Common offerings are silicone dry coating, PTFE coating, PFPE coating, special polymer coating and MoS2 dry powder coating. These are applied during the manufacturing process and bagged in a clean and efficient process, delivered and ready to be installed into application straight from the bag.
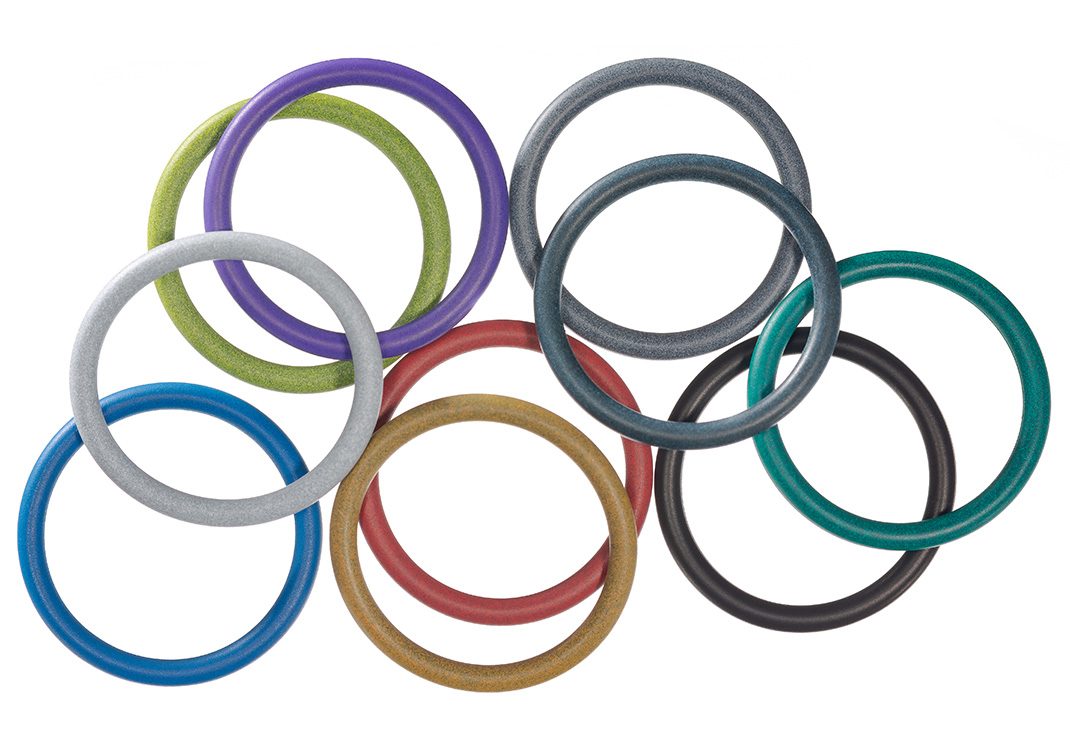
Focus on dry coatings
Dry coatings are fast becoming the coating of choice for many customers, with PTFE dry coating being one of the most popular. Most commonly applied to O-rings, the process involves the PTFE polymer being spray applied to the O-ring elastomer surface area, therefore creating a microscopic thin film layer. At molecular level the PTFE then creates a covalent like bond to the surface ensure a high quality finish.
The low friction properties of PTFE gives the advantage of low assembly forces. For example an O-ring assembled to a piston can be installed easier into the bore hardware housing mating part, therefore greatly reducing the chance of installation damage (like pinching of the O-ring elastomer material). PTFE coatings can also be used as a short term dynamic improvement to a sealing solution, as many seals suffer from the phenomenon called stick slip. This can occur where a seal has remained in the application hardware bore for a medium to long period of time and started to adhere between the surface of the elastomer and the mating metal material, causing sticking. When a PTFE coating is applied between the elastomer and the metal hardware it creates a low friction barrier, that provides a significant advantage over uncoated parts. This is because the PTFE coating generates a low friction layer, greatly reduces breakout friction and resolves the stick slip issue therefore greatly improving the performance of the application.
Because the PTFE is a thin polymer layer, coatings can be manufactured in a range of colours by adding pigment to the recipe. Typical colours include, green, blue, red, yellow and orange. By adding these colours the customer benefits from easy identification and production line inspection and furthermore allowing seals to be easily identified even once installed.