Perfluoroelastomers in valves
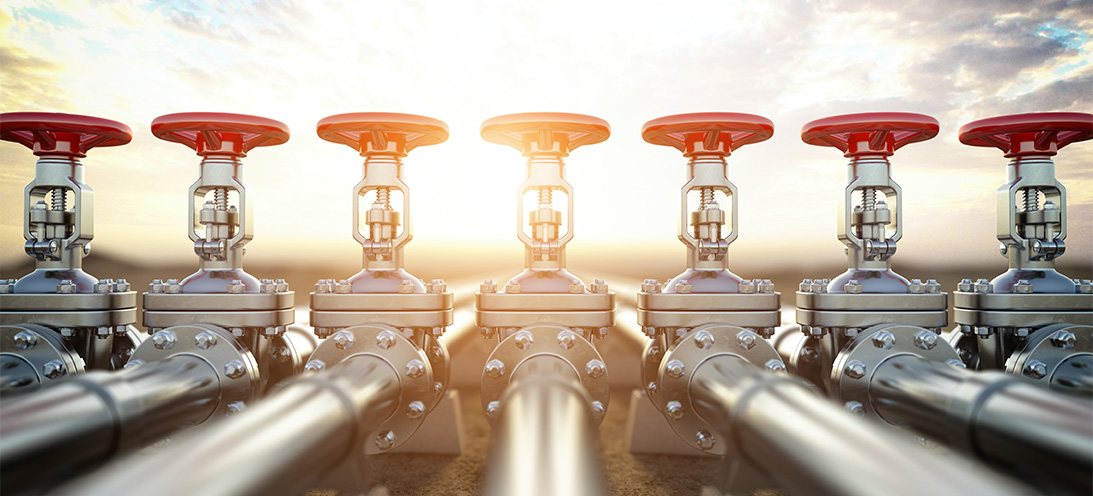
Is it time to re-visit using perfluoroelastomer seals in your valves? First developed by DuPont™ in the late 1960s, perfluoroelastomers (or FFKMs), are now widely known and understood in a variety of markets. But for those that may be less familiar with these high performance materials, here is a quick recap…
What are perfluoroelastomers (FFKMs)?
They are essentially highly or fully fluorinated compounds with a fluorine content above 75%, and they offer outstanding chemical resistance; generally better than all other elastomer types. FFKMs are often referred to as having the resistance of PTFE but in elastomer form. The term “universal” chemical resistance is commonly used; although it’s not strictly true as we will learn shortly.
Unlike PTFE, the molecular make-up of FFKM includes crosslinks (or spring-like elements) rather than just a backbone of carbon-carbon atoms surrounded by protective fluorine atoms. These crosslinks are what give the FFKMs their crucial elastic behaviour (in other words returning quickly to their original shape after being deformed). But the crosslinks are also a drawback as they can be a weak point for a chemical attack.
Different crosslinking systems can be used when developing FFKMs and the choice will determine the high and low-temperature capabilities. Compounds developed for extreme high-temperatures (up to around 325oC) generally have a less broad chemical resistance compared to the lower temperature grades (up to 225oC). Similarly, FFKMs developed to have excellent resistance to specific fluids (such as amines or high-temperature steam) can have limitations of low-temperature capability or compression set. As a result, there is no universal material that covers all application criteria bases.
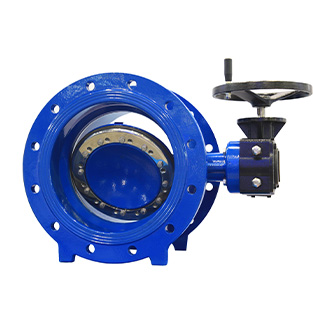
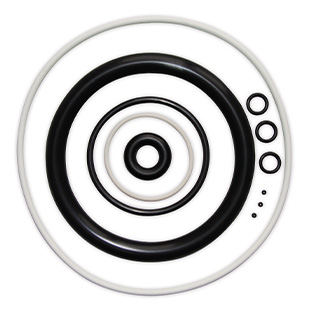
A variety of grades
Previously the number of perfluoroelastomer grades was less prolific than other elastomer types such as FKM, EPDM, and NBR, but over 50 years of technical developments have created a range of FFKM grades for specific and challenging applications; particularly in chemical process, oil and gas, semiconductor, and aerospace industries. In addition, options with a hardness range of 65 to 90 durometer, and versions that meet international standards or specifications for food, medical, CPI, and oil & gas applications means the portfolio of FFKM-based compounds available to engineers is now substantial.
In addition to technical developments, manufacturers and compounders have also been addressing the only real drawback of FFKM materials; the cost. They are difficult and time-consuming base polymers to manufacture. Coupled with a relatively low volume production base and sometimes lengthy processing times for seal manufacture, FFKM seals have always carried a high financial premium over FKM seals; even several times greater than FKM itself has over NBR.
In recent years, there’s been more focus on making general-purpose grade FFKMs with broader temperature and chemical resistance capabilities more financially attainable. The initial procurement costs remain high compared to less capable elastomer bases, but the overall cost of ownership may now be more appealing than it was twenty or even ten years ago. The ability of FFKM seals to survive for much longer in applications where exposure to a variety of fluids (perhaps wider than originally specified) is possible and considerably reduces unplanned costs associated with maintenance and downtime.
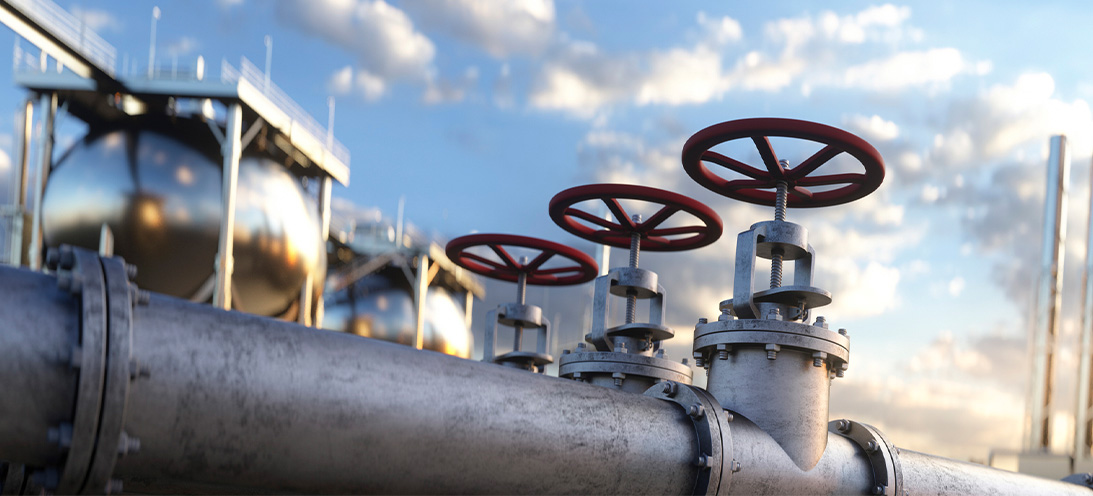
Focus on dry coatings
The cost of unscheduled maintenance and repair in pump and valve equipment can be high in any industry, but exceptionally so in petrochemical, oil & gas, and semiconductor. When these costs are fully considered in the overall lifetime of a product, the initial price of seals in a valve is considered relatively minor, but it can still be a barrier in the material selection process.
With both technical and commercial developments in recent times FFKM materials now compare more favourably against other materials for static, or low-duty dynamic applications in valves. In applications where persistent and sporadic issues keep coming back to cause problems, they are now a more financially attainable choice of material to avoid re-work, overhaul, downtime, customer dissatisfaction, and ultimately, more costs.