Rotary seals for heavy duty transportation
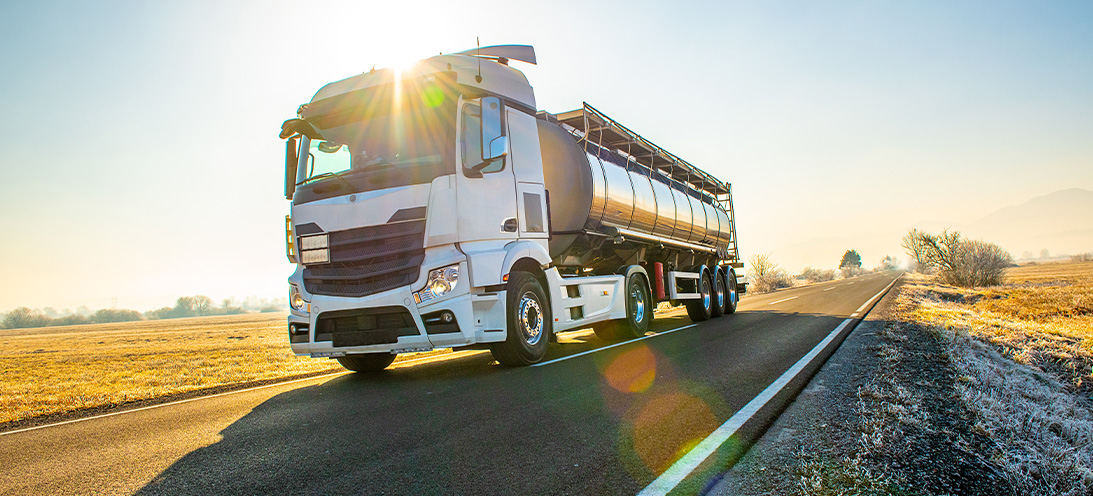
The Application
Supply Plus initially approached us with a requirement for their 2” Swing joint power spindle. In this application the outlet pipe from the fuel tank on delivery vehicles are fed into the centre of a rotating hose reel (located between the tank and cab of the vehicle), powered by an electric motor and pumped through at relatively low pressure. The current design was experiencing issues of leakage from the hose fitting in low temperatures especially at -25°C during winter, and particularly when vehicles were parked up over-night.
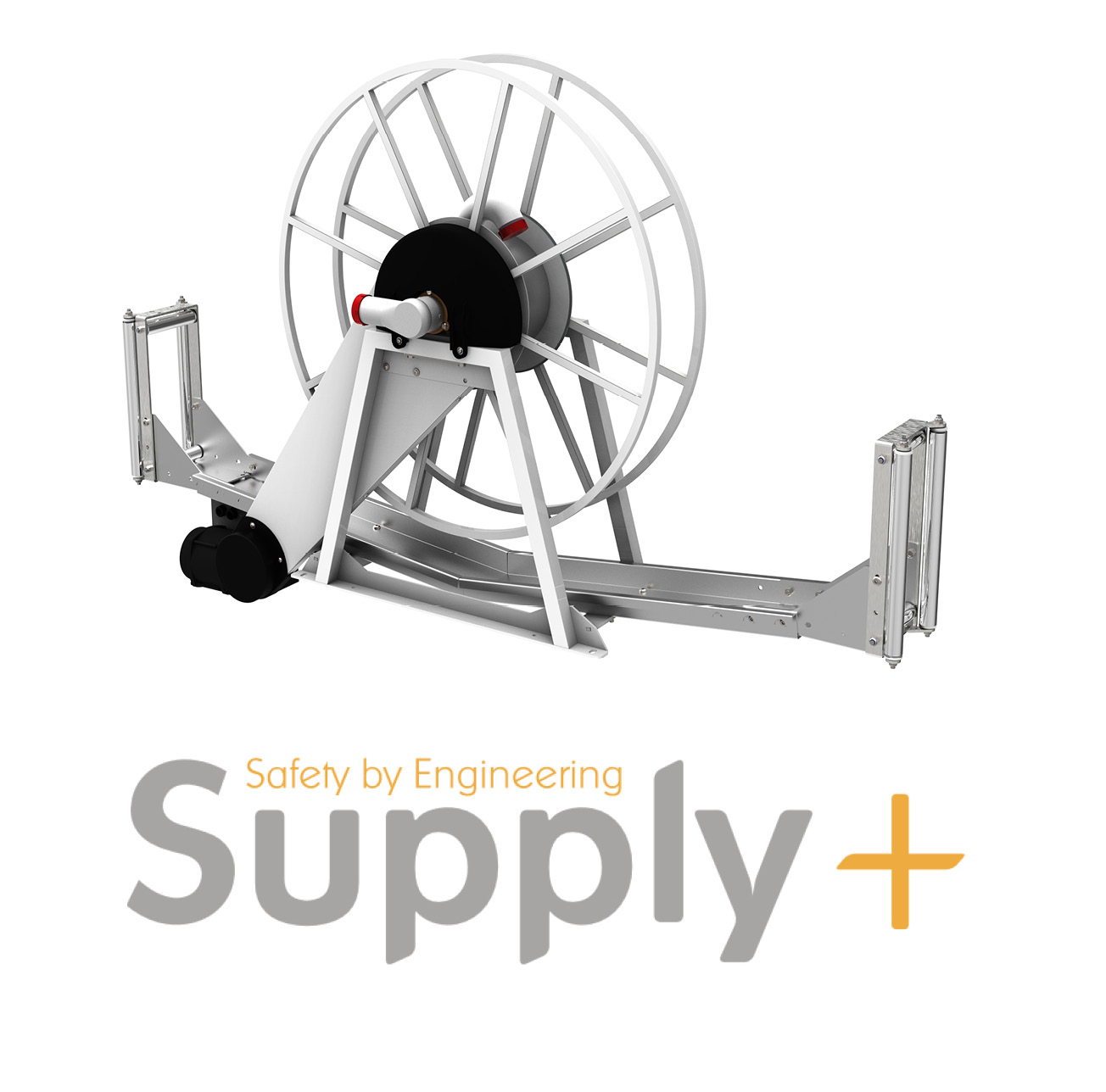
The challenges
The application required a rotary seal with low temperature capability and excellent resistance to oil-based fuels. A design was required to replace the existing seal in the available housing between the rotating metal faces and a standard spring energised rotary seal would not work in the application; a bespoke design was required.
The leakage at night when vehicles were not in use suggested the issue was worsened when the seal was both cold and not energised. We needed to design a rotary seal that would remain energised at low temperatures and low pressure.
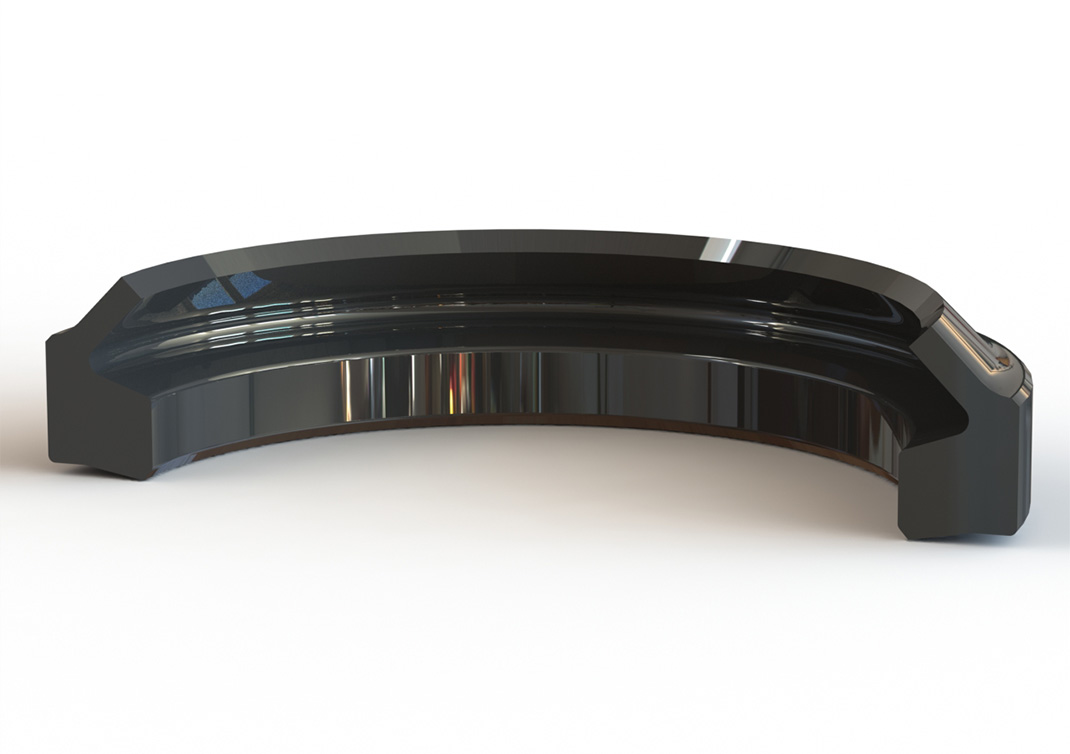
Our sealing solution
Our engineers designed a simple but effective seal, incorporating a large heel in the base of the housing that energised a lip sealing on a rotating metal face. The volume of rubber in the heel of the seal, combined with the 170° angled base created sufficient force to maintain a seal at low pressure.
We specified a low temperature Viton to ensure the seal retained elastomeric properties, applied the sealing force at low energising pressures and very low temperatures, while also providing excellent resistance to fuel oils, diesel and aviation fuel.
Prototypes were tested at both an in-house test unit and in the field for a period of four winter months. Results showed no issues during dispense of fuel and a complete cessation of leakage. The seal was approved and production orders placed, and now the design has been incorporated across additional sizes of hose reels.