Seals for Hydrogen Applications
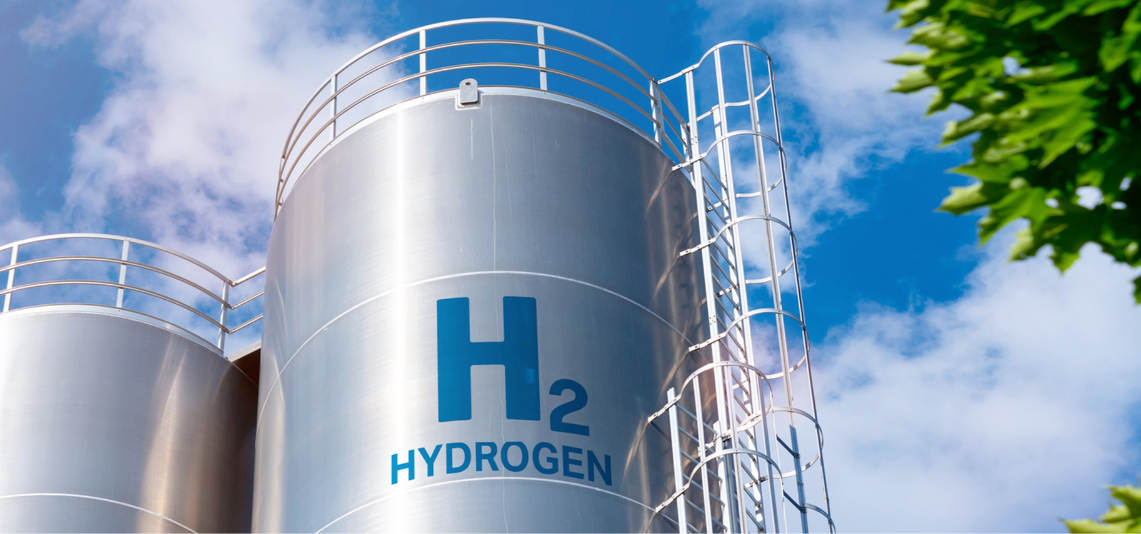
Hydrogen is the most common element in our universe, and is becoming an increasingly vital part in decarbonisation and a global sustainable energy future for our planet.
How is hydrogen produced?
Hydrogen offers a clean energy solution to parts of the economy that are difficult to decarbonise. These include industrial processes, domestic and industrial heating, and hard-to-electrify transport; including heavy-duty vehicles, ships and aircraft (where battery solutions are much less practical than they are for passenger cars). The majority of natural hydrogen is not easily obtainable and is locked away as either hydrocarbons (in fossil fuels) or water.
Extracting hydrogen from either of these sources takes energy (and a lot of it!) but hydrogen becomes emission-free at the point of use. Today, 96% of the world’s hydrogen is produced using grey and brown processes; meaning in reality it’s not very environmentally friendly at all. It is widely accepted that we need to switch to, and expand green hydrogen production. However, the electricity sources for green hydrogen (solar, wind, etc) are not always located where the hydrogen needs to be used, and cannot be turned on and off as energy demand fluctuates.
Hydrogen can be obtained in a variety of different ways, and each of these methods is generally categorised by a different colour. Grey hydrogen is produced by reforming natural gas (methane). Brown hydrogen is produced by converting carbon rich materials (such as coal) into hydrogen and carbon dioxide. These are common processed, but both result in substantial carbon emissions. Turquoise hydrogen is produced by the pyrolysis of methane at temperatures over 1000°C, with solid carbon as a by-product which can then be used or buried without emitting greenhouse gases or causing groundwater pollution. Blue hydrogen is generated by the steam methane reforming of natural gas. This generates large amounts of CO2 which must then be captured and safely stored. Pink hydrogen is created where large amounts of electricity is used to chemically split water into hydrogen and oxygen. Manufactured from a nuclear power plant, it’s free from ongoing emissions (other than those emissions produced in building the nuclear power station). The oxygen can be used by industry or vented to the atmosphere, with no negative effects to the environment. Green hydrogen is also produced by electrolysis of water, but the electricity required is taken purely from renewable sources such as solar, wind, tidal and geothermal processes. This is widely regarded as the ONLY totally clean hydrogen extraction method.
Today, 96% of the world’s hydrogen is produced using grey and brown processes; meaning in reality it’s not very environmentally friendly at all. It is widely accepted that we need to switch to, and expand green hydrogen production. However, the electricity sources for green hydrogen (solar, wind, etc) are not always located where the hydrogen needs to be used, and cannot be turned on and off as energy demand fluctuates.
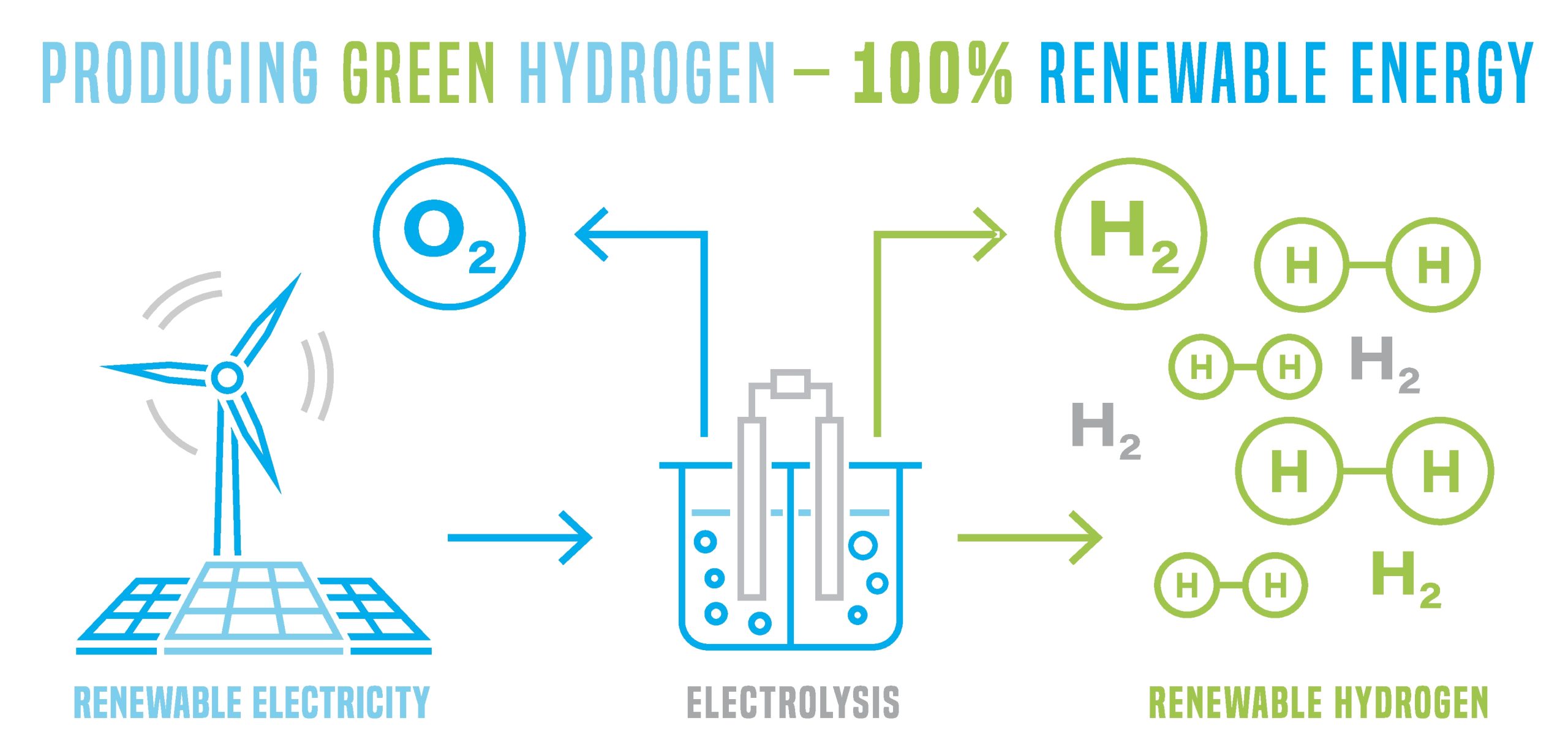
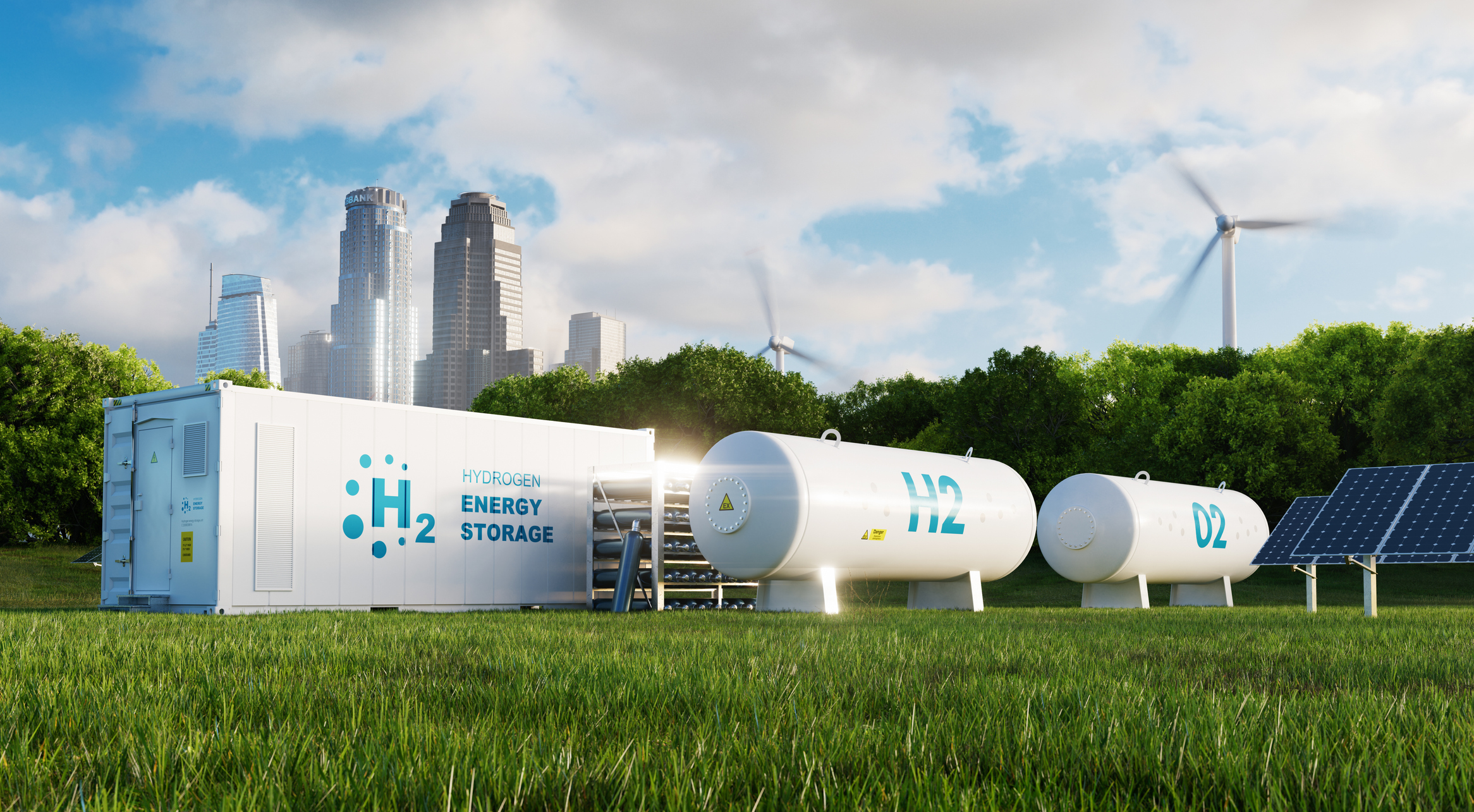
Engineered seals for hydrogen applications
Sealing hydrogen presents a number of challenges and we need to consider the following parameters when designing a sealing solution.
When it’s a gas we need to consider the gas permeability of the sealing materials with pressures of 700 bar or more. We also need to consider the tightness of the static or dynamic sealing surfaces – including surface finish requirements for the mating components. As a compressed and cooled gas, pressures can be up to 1000 bar in conjunction with temperatures down to -240°C. When it’s a liquid, the sealing solution needs to be suitable for the associated cryogenic temperatures of -253°C (although pressure regimes are generally less than 5 bar in these conditions).
When hydrogen is within a carrier, the chemical compatibility requirements of the carrier medium (such as ammonia or liquid organic hydrogen carriers) need to match the sealing materials specified.
Electrical conductivity or resistivity requirements, together with cleanliness and purity, may be required for sealing materials used in electrolysers and fuel cells.
Chemical and temperature compatibility with all the media associated with hydrogen production, transport and conversion processes, including all by-products, emissions, cooling fluids and electrolyte materials.
For seal applications in hydrogen with no particularly high demands in any one area, EPDM elastomer based solutions can often be the most cost effective. For permeation resistance, we can offer chlorobutyl elastomer or polyurethane seals. For high pressure applications, elastomers or polyurethanes with high extrusion resistance and resistance to rapid gas decompression, or PTFE which is not affected by RGD, can be used.
In electrolysers and fuel cells, the purity and cleanliness requirements can be met with materials and treatments we frequently use within the semiconductor market. For applications below -60°C, elastomers become hard and brittle, but PTFE, PCTFE and metal sealing solutions can be used down to cryogenic temperatures. For high temperature applications, some FKM or even FFKM elastomers can be used up to 220°C or even 300°C but the normal preference here would be PTFE sealing solutions.
Metal seals are capable of even higher temperatures up to around 870°C. Metal seals can also have soft coatings such as tin or indium to achieve gas tight sealing, or gold or silver to reduce the risk of hydrogen embrittlement.
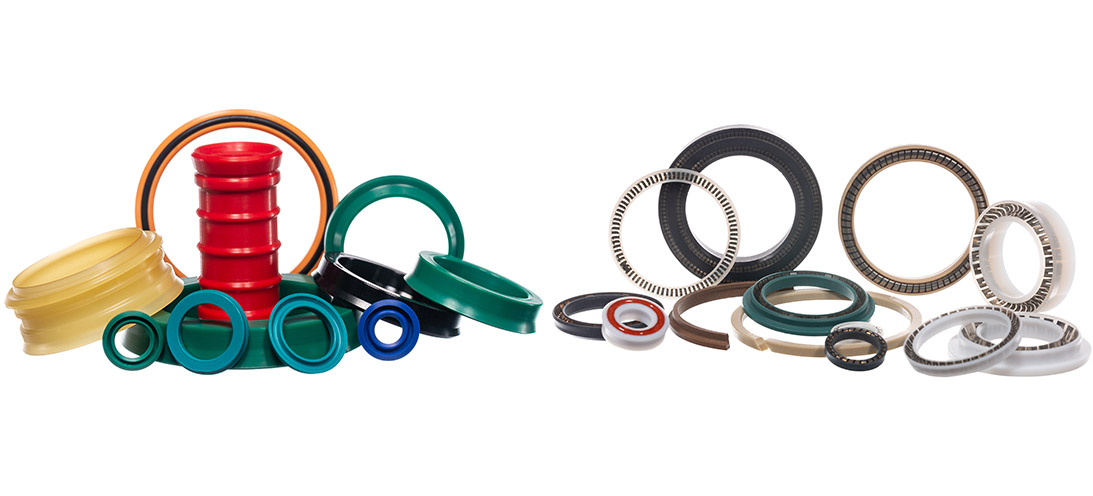
The evolving hydrogen industry
The hydrogen industry is technically vast and challenging for sealing applications, covering both extremes of temperature, alongside demanding pressure and chemical resistance requirements, coupled with stringent leakage limits and associated safety requirements.
Applications typically demand long service life and in certain cases require parts with high levels of technical cleanliness and purity. With requirements for elastomer, polyurethane, PTFE and metal sealing solutions, full consideration of the application is essential to select the most appropriate seal design and materials.