Seals for Semiconductor Applications
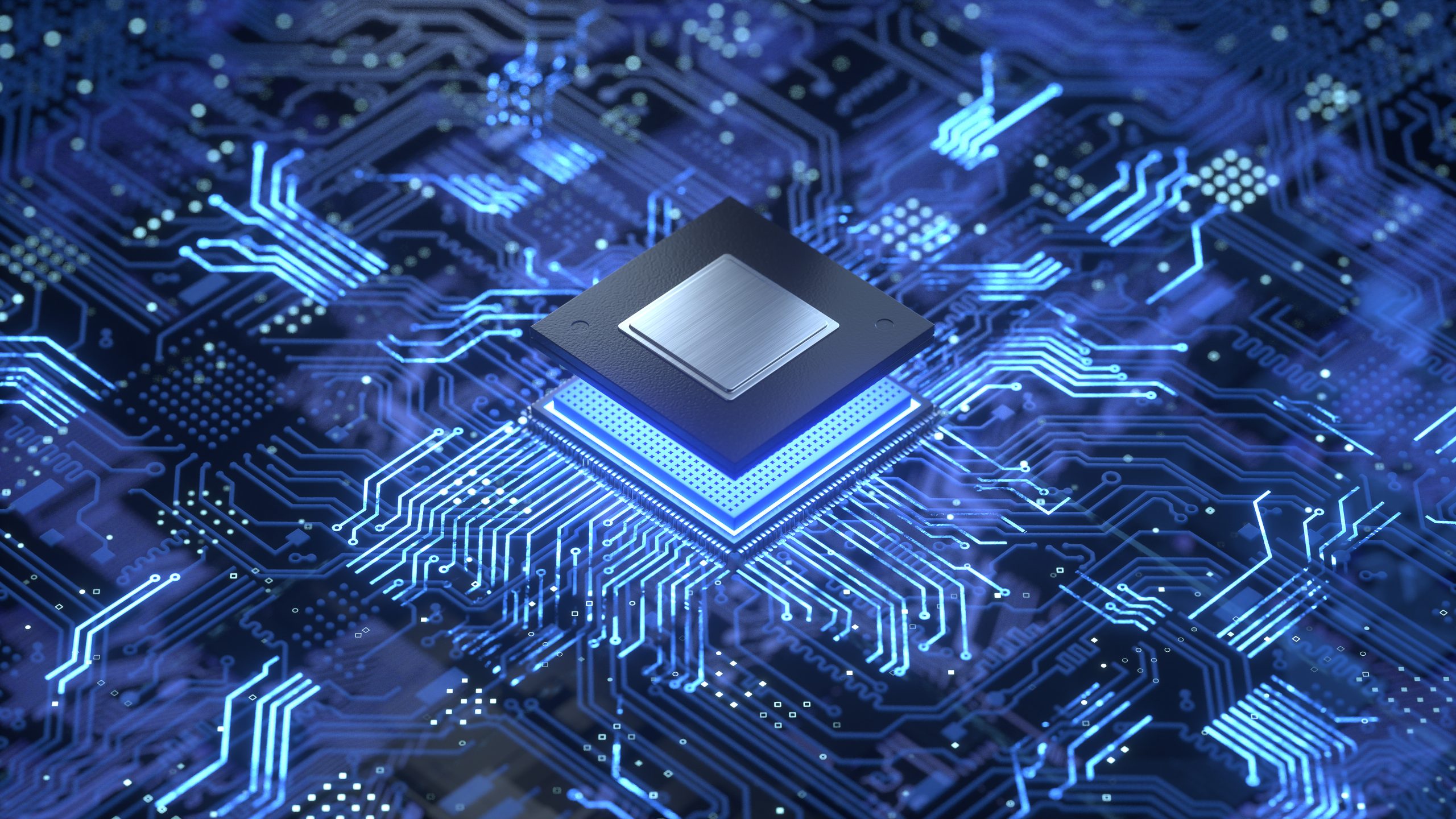
Characteristics of Semiconductor sealing
The technology push for more complex devices requires semiconductor companies to research and design new methods of processing within their manufacturing cells. This brings an increase in challenging technical conditions including complex chemistry, increased temperatures and stringent cleanliness within manufacturing process and the surrounding tools.
This challenge is passed to the component and material suppliers who must adhere to the same rules to ensure all the criteria for these new processes are met even under the combined effects of the outlined above conditions.
In our world of performance materials for the semiconductor industry, it becomes clear that materials that have been formulated in the past for older generation tools may not be technically capable in new and future applications, and therefore it is paramount to investigate and formulate new performance materials that meet each specific application.
Wet Cleaning and ECD
Wet cleaning is a method used in semiconductor manufacturing to remove any contaminants from each layer of the wafer surface, usually by using chemicals and pure water. ECD is a method of laying down the bulk of the copper wiring within a semiconductor device.
Compounds for wet cleaning are engineered for static and dynamic applications with minimal metallic ion contamination.
Thermal applications
Compounds for these applications are required to have excellent thermal stability and maintain integrity at elevated temperatures often found in processes such as Oxidation, Diffusion, Annealing, and RTP.
These processes are extremely challenging for seal materials. High thermal load at 300°C with temperature cycling can encourage compression set, and they must also be manufactured to limit out-gassing at high temperature to prevent contamination within the process area and offer superior physical properties.
Thin Film and Dry Etch
Thin film deposition is the process of creating and depositing thin film coatings onto a substrate material. These coatings can be made of many different materials, from metals to oxides to compounds. Dry etch is a process for material removal. Thin Film applications such as HDPCVD, PECVD, SACVD, PVD and ALD, along with Dry Etch and Ashing processes present harsh plasma and gas environments, often at elevated temperatures.
Where traditional seals might deteriorate and fail in these conditions, our next-generation compounds have excellent chemical and thermal resistance, and are virtually impervious to extreme fabrication processes.
Plasma processes are a very hostile and aggressive environment for seal materials. The corrosive chemistry at temperatures up to 250°C means that compounds must be chemically and thermal stable across the operating range and must include low-outgassing and low particle count features. These applications are varied; from window and door seals, chamber lid seals, valve seals, exhaust flange seals- each requires application knowledge to ensure all technical parameters are met before materials are recommended.
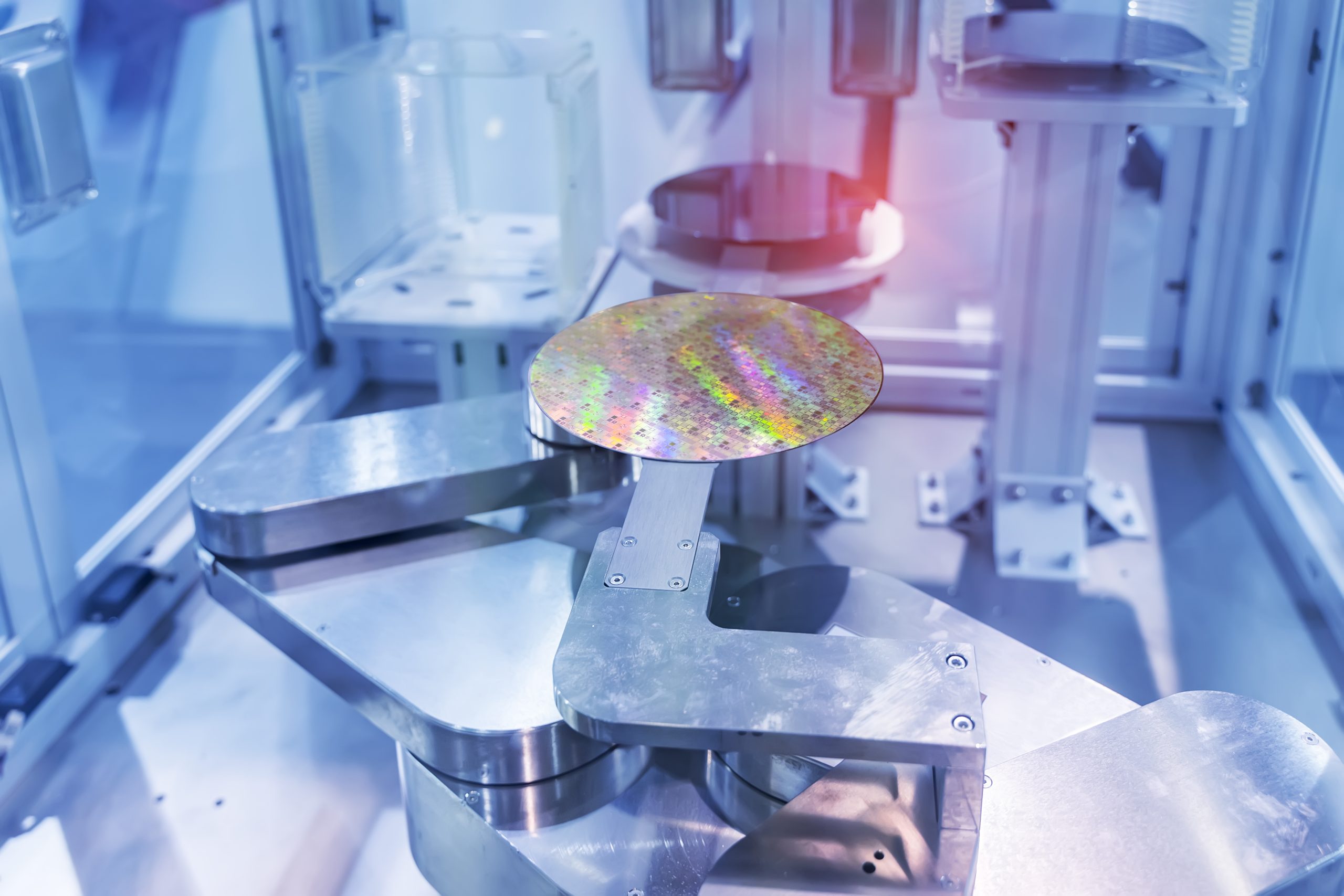
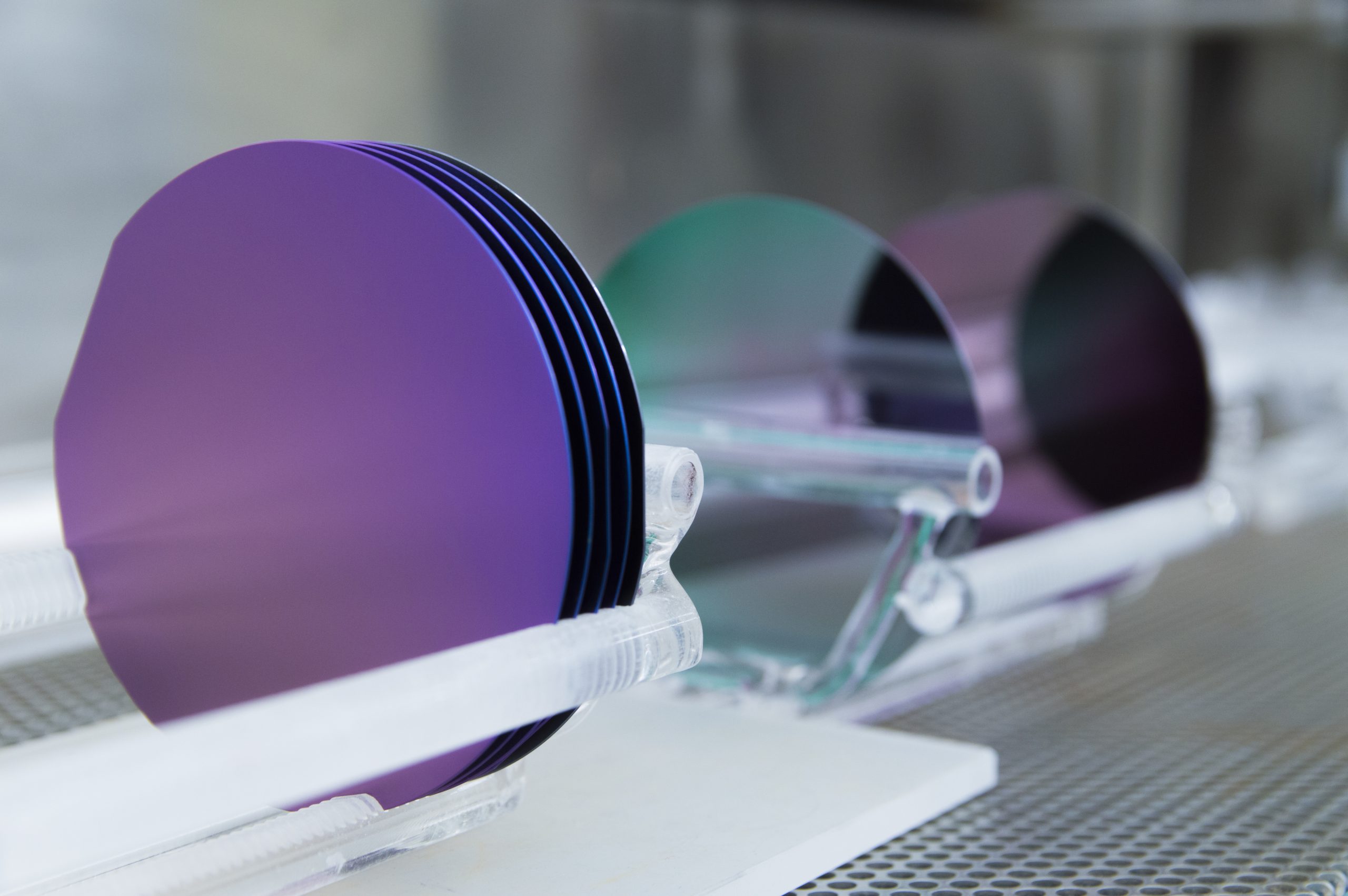
Ultra High Purity (UHP) materials
Perfluoroelastomer materials
FFKM’s contain fully fluorinated polymer chains, and offer the ultimate performance from an elastomer for applications where the seals are exposed to high temperatures and aggressive chemicals for plasma, wet and dry, semiconductor process applications. There is an extensive range of FFKM materials available; the challenge is choosing the correct material grade for an individual application as one perfluoroelastomer will not cover the broad spectrum of requirements across all semiconductor process conditions. For example, some materials are better than others at high temperatures, some demonstrate better chemical resistance and some are poor at thermal expansion.
Several compounds within our range of PERFREZ® perfluoroelastomer materials offer the best performance characteristics based on high thermal values, excellent low out-gassing and low particle count. We also offer a hybrid material which is an excellent “all-rounder” as it’s chemical formulation falls between FKM and FFKM. This means it performs consistently under slightly less demanding application conditions and with the added benefit of lower cost of purchase versus ultra-high grade FFKM’s.
Other compounds within our range are very specific to semiconductor process applications such as CVD, PVD, Plasma Etch (oxide & metal), fluorine and oxygen compatibility with a high temperature threshold material for sub-fab NW /ISO exhaust line environments. As new challenging processes emerge within the semiconductor industry, further progress in high temperature materials above 300° C will be developed; we expect to add a new generation material for plasma applications to our portfolio of materials by the end of 2022.
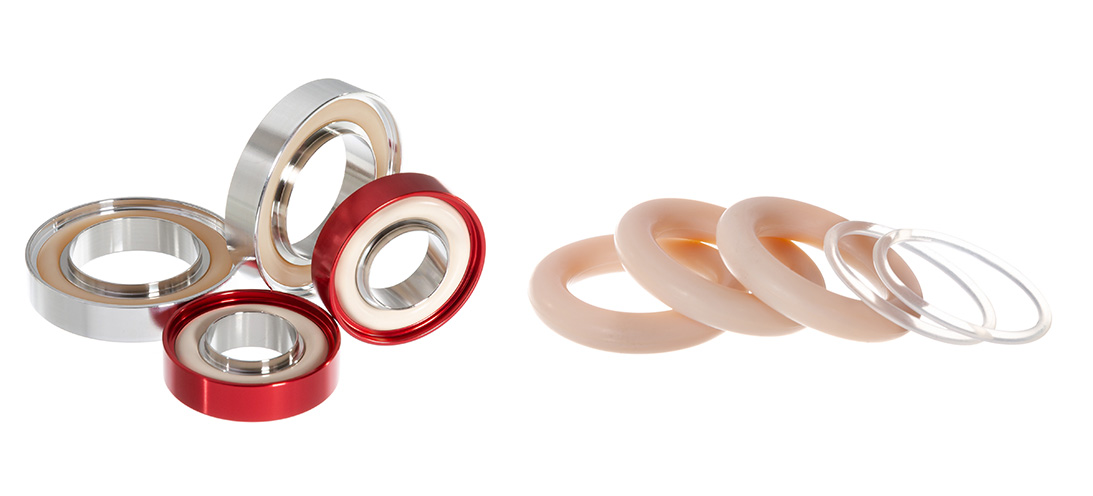
Cleanroom Manufacturing
Semiconductor cleanrooms must be designed to control static, out-gassing, and any contamination from external particulates such as dust, dirt, airborne microbes, and aerosol particles. Just a single particle of dust or debris on a wafer or component is enough to cause a catastrophic defect (that will ultimately lead to failure of a device).
It is created and maintained by removing the air, circulating it through a filtering system and distributing (the clean and filtered) air back into the cleanroom environment. This can be achieved at varying levels of cleanliness, and it depends on what is specified for each individual manufacturing environment or the finished product requirements. Different cleanliness levels are classified by the concentration of airborne particles within a measured space.
As well as the manufacturing environment for the semiconductor itself, it’s important to ensure any auxiliary products (such as seals) brought into the environment also maintain the same levels of cleanliness.
We provide a complete cleanroom production process; from material blank production through to inspection and packaging using controlled materials within state-of-the-art cleanrooms. Our clean room manufacturing facilities are Class 7 (10,000) manufacturing and Class 5 (100) inspection, cleaning, & packaging.