Silicone O-rings for De Soutter EcoPulse™ lavage system
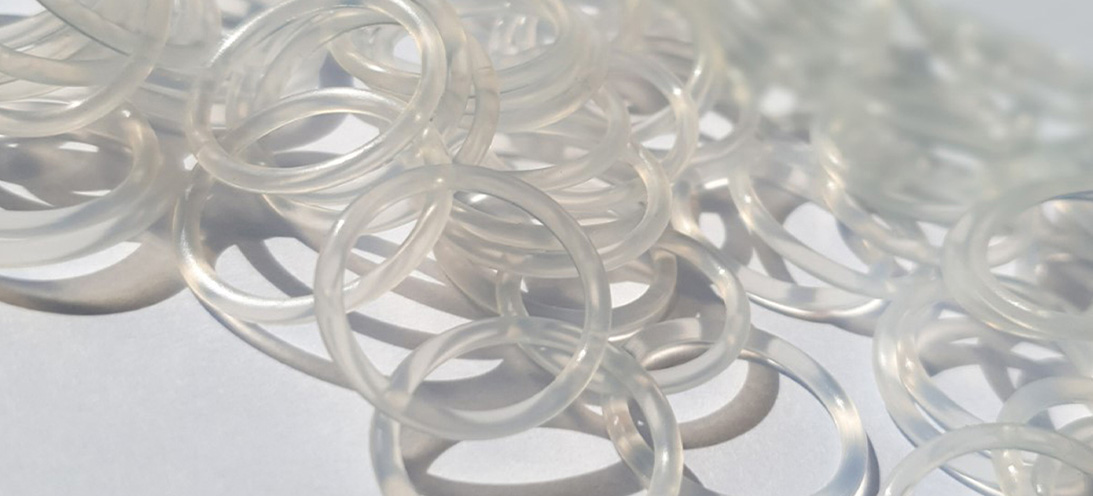
De Soutter Medical Ltd specialises in the development, production and worldwide distribution of high performance orthopaedic tools for surgical procedures, offering their customers a comprehensive range of technically innovative and high quality products.
The application
De Soutter Medical recently launched their new EcoPulse™ lavage system for use in orthopaedic surgery.
The EcoPulse™ connects onto the front of a reusable De Soutter handpiece, and allows surgeons to lavage the surgical site using saline water. It can simultaneously be connected to a suction device to remove waste from the surgical site. The EcoPulse™ is supplied as a single use sterile packed product, with a range of nozzles available for specific surgical procedures.
The new EcoPulse™ has a pared back functional design to eliminate superfluous plastic, and instead of using disposable batteries (and the associated single use wiring and motors) it connects onto a reusable power tool that is already being used to perform the surgical procedure.
This eliminates a large amount of clinical and WEEE waste, and compared to other products in the market reduces clinical waste by up to 60%.
We were approached to manufacture two different sized o-rings for the ECO Pulse upgraded design.
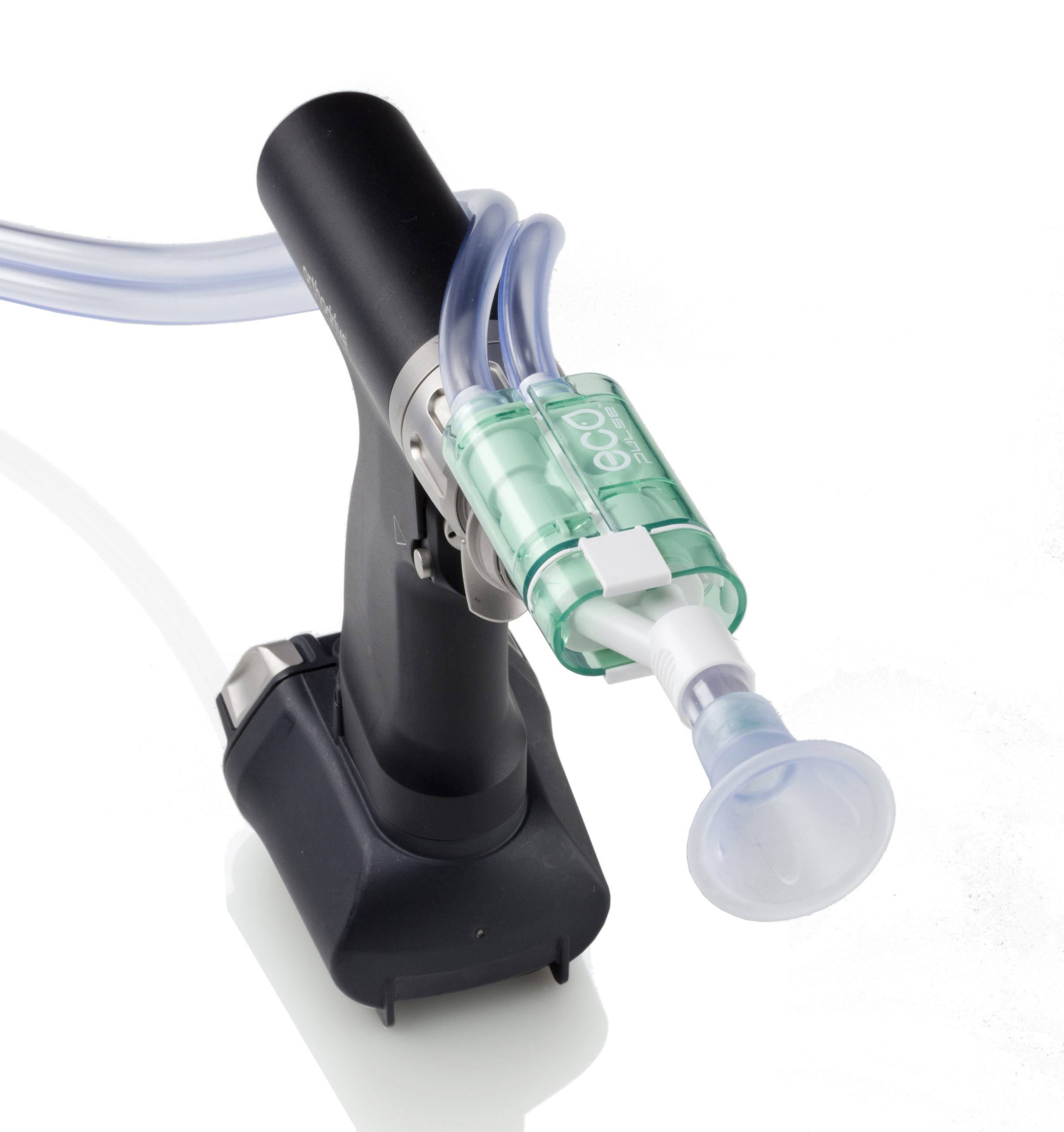
Our sealing solution
The seal application was located within the disposable pump/irrigation attachments to ensure that no saline water leaked, and there was no loss of suction during use.
The application was relatively straightforward in terms of mechanical sealing, but due to the nature of the product there were critical demands on the material and during the manufacturing process.
For material selection our engineers specified a USP Class VI translucent silicone; suitable for medical devices due to its biocompatibility features and resistance to bacterial growth.
The (bespoke and dedicated) moulding tool was coated in titanium nitride, so the use of release agents during the manufacture process of the O-rings is not necessary. This is to mitigate the risk of any cross contamination with the O-rings; this is especially important when producing seals used within devices where there is any risk of patient fluids crossover.
Cleanroom manufacturing and the O-rings are double bagged packaging in order to avoid any cross contamination. These parts are manufactured and packaged at our ISO13485 approved manufacturing site to achieve these requirements.
Customer satisfaction
Working in conjunction with our valued customer De Soutter Medical, we assist with design support and technical recommendations on the development and manufacture of sealing products for use within their medical devices.