Why use Push-in-Place gaskets?
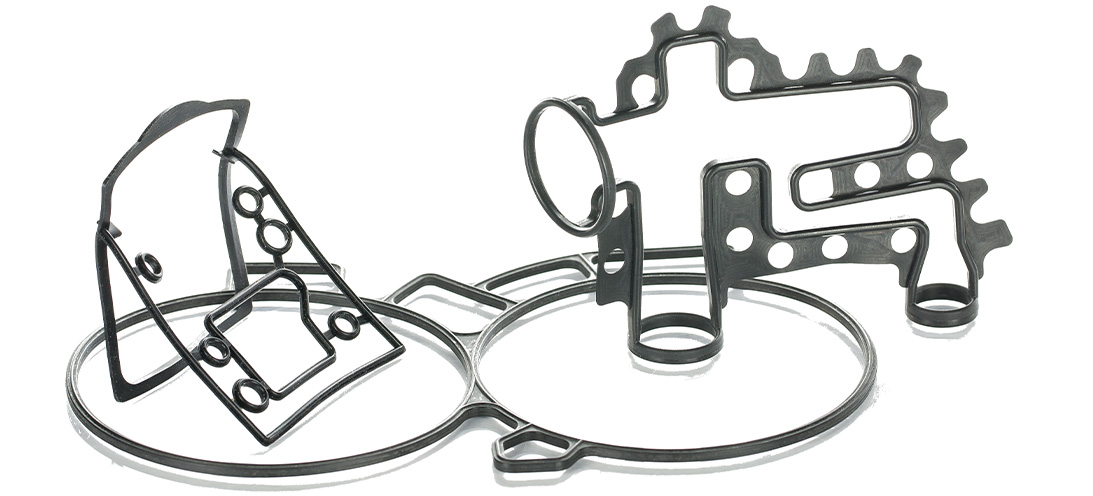
Gasket sealing overview
There are many ways to seal the static join between two components. Whether this is to keep fluids inside a cavity or to keep fluids or contaminants out of a device or assembly; the options can vary from simple O-rings, moulded elastomer gaskets and flat sheet style materials, to liquid gaskets (or RTV’s).
As with all sealing applications, the optimal sealing solution is designed by first reviewing the application conditions. These include temperature, pressure, fluid exposure etc; and other variables such as life requirement, equipment serviceability and seal compression set should all be considered. Arguably though, compared to other sealing applications, when designing face, cover or flange sealing solutions it is imperative to consider the packaging requirements and assembly issues of gasket sealing options. The need to avoid or seal around bolt holes (or other retaining/clamping devices), together with optimizing hardware wall sections or depths can play a very important part in choosing the most suitable gasket sealing technique.
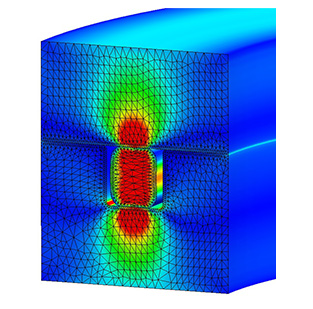
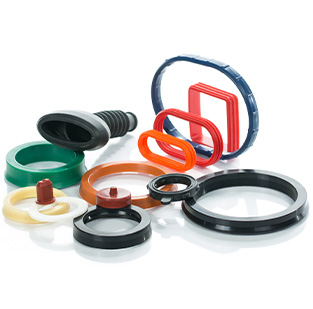
What are Push-in-Place gaskets?
With the right combination of application conditions, an o-ring style approach to sealing may be the most appropriate. O-rings tend to require relatively shallow grooves compared to their cross section in one half of the assembly, and in cases where the groove is round in plan view – they can be a good solution.
However, in cases where the groove follows a more irregular path or profile (frequently referred to as a “racetrack”) the o-ring can sometimes pop out in places – often where the two housing parts are being brought together. A common solution is to design a custom moulding that has the same profile as the centre line of the racetrack groove and simply drops into place.
A similar approach is used when the application or hardware constraints steer the design towards a gasket that has a greater cross section depth compared to the width; this would typically be designed so the centre line of the gasket matches the centre line of the groove plan profile – again so that it drops easily into place.
An inherent problem with gaskets that can drop into place is that often, they easily drop out of place too. If the component needs to be inverted, or has the potential for rough handling during assembly then the gasket may become partially or fully dislodged from the groove, which results in a badly sealed interface. The best solution to this issue is to incorporate retention pips or bumps in the gasket design, a solution known as Push-In-Place (PIP) gaskets. These require a distinct force to put them into the groove, and as a result require more than just gravity to get them out of the groove.
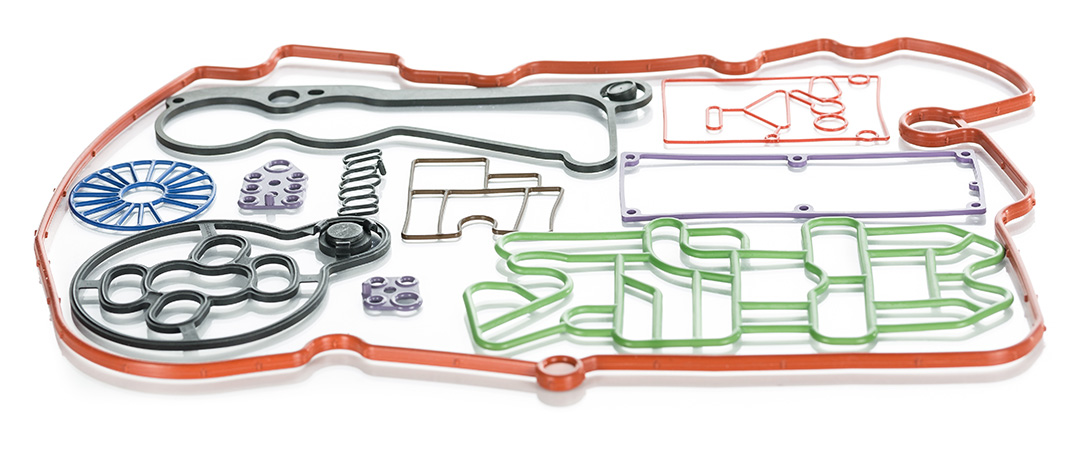
Why use Push-in-Place gaskets?
There are other less effective solutions for tricky groove sealing, such as the use of a sticky grease, or the use of an adhesive. These can bring compatibility and health and safety issues to consider, and carries the risk that any contaminant could keep the gasket off the surface that it is supposed to be sealing against, and the integrity of the seal can be severely compromised as a result.
Neither of these approaches can be recommended, and instead the use of retention pips is a safe and secure way of ensuring the gasket remains in the groove.
To determine the optimum number, size and position of the retention bumps, Finite Element Analysis is used to ensure that they provide sufficient squeeze to prevent the gasket being easily dislodged, whilst not overfilling the groove space with seal material or interfering with the seal compression footprint against the hardware faces.
The bumps can be strategically positioned to control any distortion of the gasket under pressure or temperature conditions. For example, low temperature conditions can shrink the gasket and tighten the radius it adopts around a bend in the racetrack profile. This can reduce the seal compression locally and potentially create a leak path.
By positioning retention bumps at either end of the bend, the thermal contraction can be controlled to minimize the risk of leakage. Effective retention ensures that if the part needs to be inverted (which could be the preferred assembly method for practical reasons), or is subject to rough handling – the gasket remains correctly located in the groove.
For large gaskets this is normally the most effective solution; and on smaller gaskets (particularly those located well inside the periphery of the assembly) there is a significant risk of a dislodged gasket being totally undetected unless using a PIP gasket design.
It is possible to include tell-tale signs on a gasket design. For example, if a part of the elastomer gasket protrudes sideways through a gap in the housing wall the presence of the gasket can be checked – either with the human eye or an automated vision system. However this does not ensure correct seating all around the gasket length, and cannot be used for internal gasket locations. In these cases a missing or badly fitted gasket would only be discovered during post-build testing, or even worse with a machine failure at a customer.
If included at the design stage, the small additional tooling and material costs associated with a PIP gasket are negligible compared to the costs of an impossible assembly scenario, strip and re-build costs on the assembly line, or the consequential costs associated with failure of an assembly once delivered to a customer.