The Technical Hub
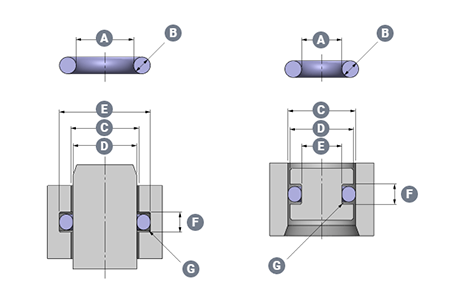
O-Ring Calculator
This interactive calculator assists engineers with selection of O-ring and hardware dimensions, and to form the basis of an O-ring installation.
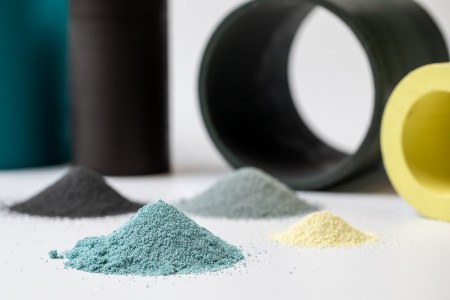
Chemical Compatibility Checker
This interactive guide will help you choose a seal material based on existing compatibility test results of known chemicals and elastomers.
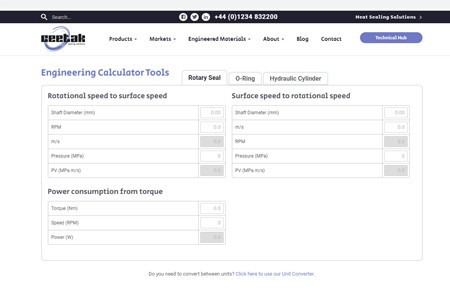
Interactive Engineering Calculators
Click here for volume, mass and compression set values for O-rings and rotary seal and hydraulic cylinder calculations.
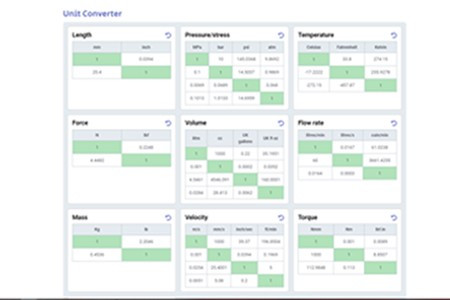
Unit Converter
Our interactive conversion tools allow engineers to switch between units of measurement when preparing engineering calculations.
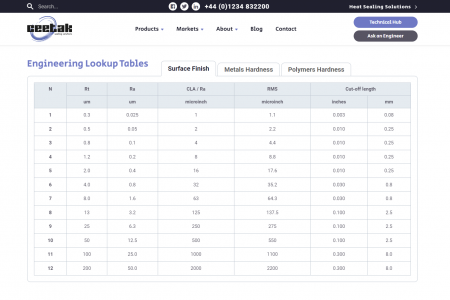
Engineering Tables
Our reference tables provide cross reference information for surface finish, metal hardness and polymer hardness measurement units.
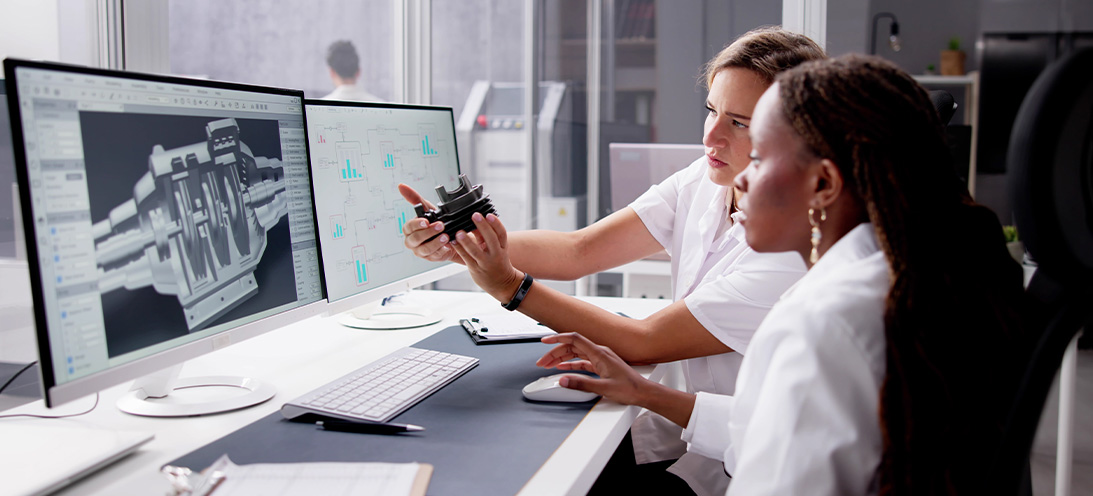
Tools
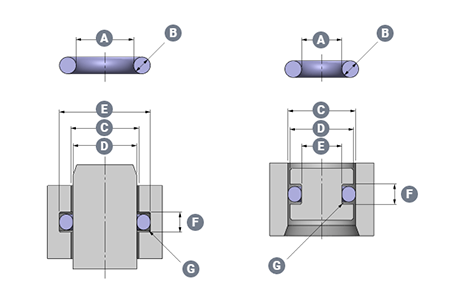
O-Ring Calculator
This interactive calculator assists engineers with selection of O-ring and hardware dimensions, and to form the basis of an O-ring installation.
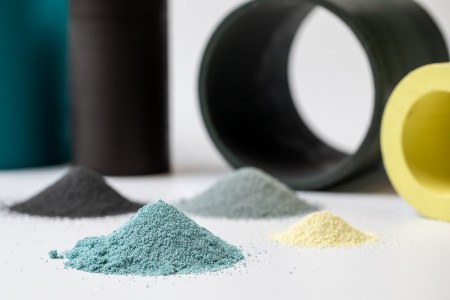
Chemical Compatibility Checker
This interactive guide will help you choose a seal material based on existing compatibility test results of known chemicals and elastomers.
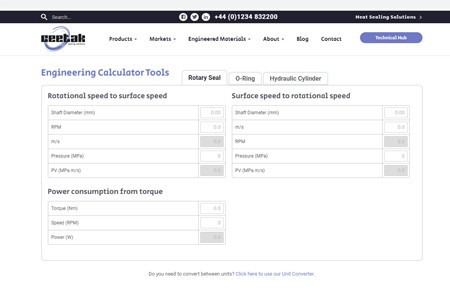
Interactive Engineering Calculators
Click here for volume, mass and compression set values for O-rings and rotary seal and hydraulic cylinder calculations.
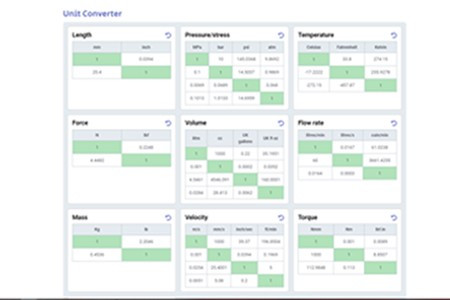
Unit Converter
Our interactive conversion tools allow engineers to switch between units of measurement when preparing engineering calculations.
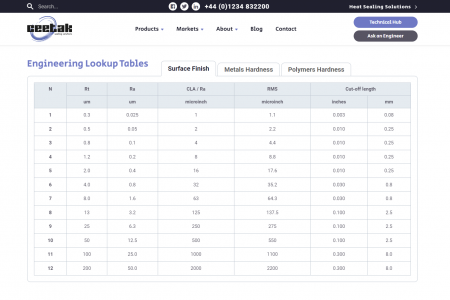
Engineering Tables
Our reference tables provide cross reference information for surface finish, metal hardness and polymer hardness measurement units.
Articles
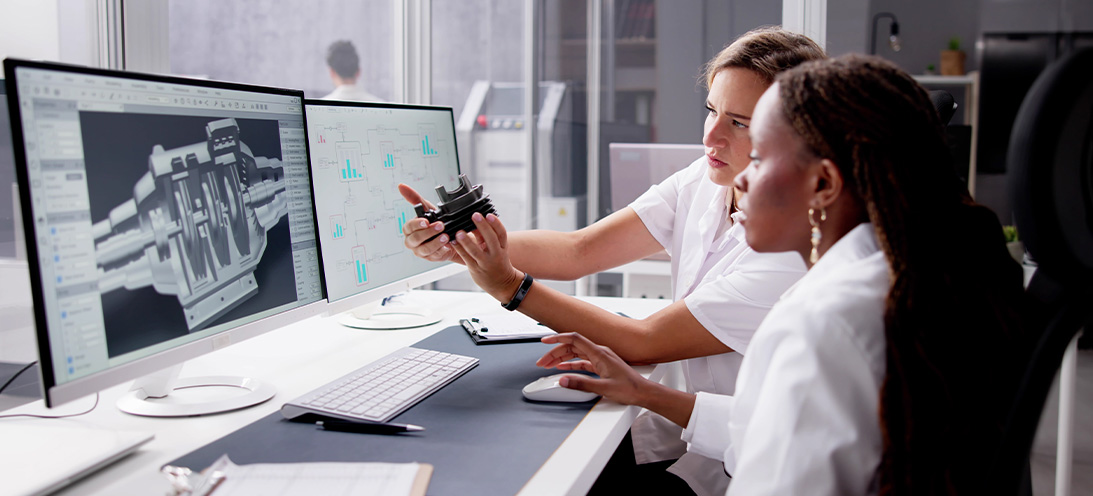